Complete event of rebuilding the Storebro 34 Building number 1434
After rebuilding a 28 foot wooden motor sailor with my neighbor Jan, we realized we liked to work with wood, and restoring old boats and decided to look for a boat for me. Since sailing is not exactly my cup of tea I was looking for a classic wooden motor boat. To make a long story short, I found a classic Storebro 34 motor boat dating from the seventies which "needed work". The expression "needed work" was an understatement when looking at the wood rot and the holes in the hull on the bow and the stern.
In contrast to the motor sailor, which was build using three layers of mahogany plywood in diagonal planking, resulting in a cold molded hull of 1.5 cm thickness, the carvel built hull of my Storebro is made up of massive mahogany planks of 3 cm thick. Therefore, the techniques I will be using for this boat are quite different from the skills we learned from the former project.
Although the winter time is not the ideal time to inspect and buy a boat we went over and were pleasantly surprised by the lay out of the Storebro 34 and the standing height in the main cabin.
The aft cabin is much lower but since it is mainly a bed room with two beds it comes over very comfortable.
The boat was bought and it was decided to sail the boat from the south part of Holland to the area where we planned to do the needed maintenance of the boat.
While I was for my work abroad Jan made a second visit to prepare the boat for travel over the Dutch water ways. I received a picture from him which made me not very comfortable for sailing the boat over and it was than decided not to sail the boat over the Dutch water ways in the beginning of May 2010.
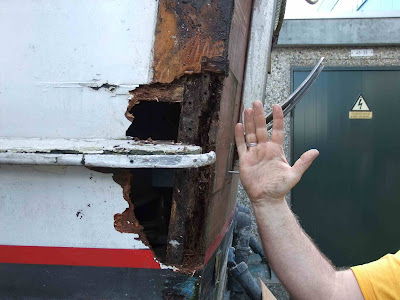
The decision was than made to transport the boat by road to the area where I live. Arrangements were made and the boat was loaded on a truck and transported to the yard
To start with some additional information about the actual boat it is built in 1969 or 1970, this according the production number, 1434, which can be found on the floor boards and seat support gratings.
From this type of boat are a total of 1230 built between 1965 and 1988 original in wood mahogany on oak frames.
In 1969 the hull was changed from wood into GRP but there were still mahogany hulls available until 1978.
The overall length of the boat is 10.35 meter
The beam is 3.2 meter
The draft is 0.9 meter
Displacement between 5 and 7 ton.
The dash board is still original of this boat and has 4 handles for the propulsion, two for regulating the speed and two for the clutch.
For the rest all gauges look original.
Going over the different web sides available as well as the original brochure of the boat it shows that most of the boat is still original as built.
The bathroom, which not only holds the toilet but can also be used as a shower furthers a sink, is installed.
The aft cabin holds two beds one on port side and one on starboard side with a storage cabinet in the aft between them. This cabin is lower than the rest of the boat and one can not stand straight up comfortable.
The main cabin is of the height that one can stand comfortable and holds the kitchen and seating area which can be concerted in a sleeping bed as well.
Kitchen is equipped with a small sink and a Taylor Paraffin cooker which I will leave in place since at the moment I do not see a place where I can create safely a gas bin.
View from main cabin into the steering cabin.
Second inspection
The Bow
After the boat was delivered and properly positioned as well as supported it was time for the first decent detailed inspection.
As with all boats the second more detailed inspections shows more parts not as good as one would expect.
In this case more rotten wood was found and although some of this was expected it is always a kind of disappointment to find more work than original anticipated.
During this inspection it was found that repairs were made in a poor and unacceptable way and actually there were more cover ups for rotten wood than actual repairs were done in the past.
Wood was placed over holes in the stern side and bow side, the ones of the stern side we were aware off but the ones of the bow came as a bit of a surprise.
Originally it looked like at the bow side that this was original as built but unfortunately after removing some wood and stripping some paint is showed that rotten wooden mahogany planks were removed and inserts were made of Plywood.
Most likely this is also the reason that the bow is starting to separate during the drying process of the boat since it shows that there is no proper connection made between the original mahogany hull, ply wood and the frames of the boat.
The Stern
Most of the hull is in a reasonable condition and the worst parts are the aft corners between the sides and the stern of the boat.
We were aware of this fact and to perform the necessary repairs on these parts did not came as a surprise. After some more detailed inspections of the first area to be repaired a plan has to be made. First all hardware was stripped of the deck while at the same time measurement and pictures were taken of the position of all installed hardware. The idea is to bring the boat in an original condition with the same hardware on the same position as been found. Then comes the moment that the actual dismantling of the boat has to start, which is actually one of the biggest decisions to be made when one starts a project like this. When that decision has been made all comes natural . A process is started which can not be stopped anymore till one is finished. Since we wanted to start with replacing the wood of the aft hull sides where it meets the stern the aft cabin was stripped at the inside. This went reasonable easy since the panels were screwed against the frames.
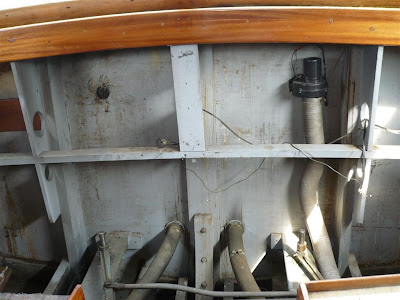
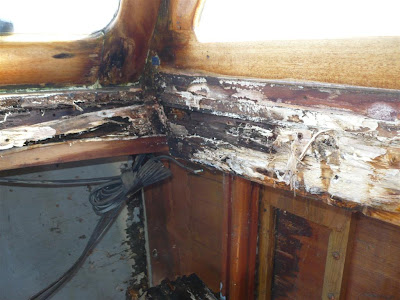
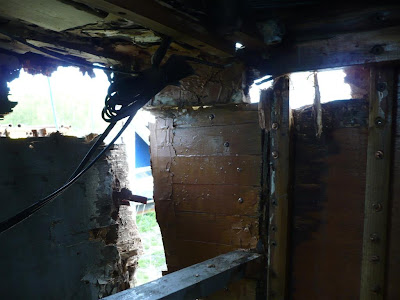
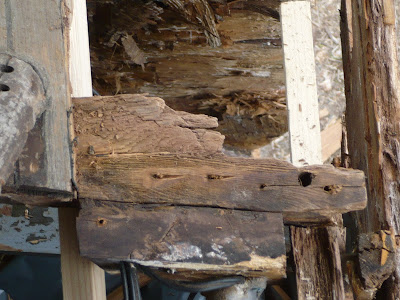
As can be seen from above pictures more rotten wood was found and actually all deck support have been rotten away or were penetrated with water. The result is that we also had to replace the deck support beams from the stern to the bow as well as the ones of the transom aft.
After removing some of the teak deck aft and on the sides of the boat the actual repairs started with the port-side aft hull.
First with an electric saw we started to remove the planks between the frames and at the same time checking how far the rot had entered the mahogany hull planks.
For complete removal of the planks also the rivets have to be removed where the planks are connected with to the oak frames. Methods used for removal and installing rivets will be discussed in a later stage.
Start of the Repairs
As can be seen from above pictures we found some surprises in the form of old repairs with wood, plastic bag, epoxy and other unknown types of filler.
To make a good connection between old and new wood and to make sure that the frames remained in the same position wood was cut out plank for plank while new wood was inserted . The to be removed planks were cut out with a circular saw which was adjusted in such a way that the saw would not cut deeper than 96% of the hull plank thickness this to prevent that the saw would cut into the frames and damage them. The circular saw was guided to get straight saw cuts, otherwise it would be very difficult to fit the new planks.
The last millimeter of the wood was cut with a multi tool, before the old wood was removed.
Cuts were made in the form of so called pie point this to make sure that new and old wood would have a good long glue connection as well as that old and new wood where the connection was made would be supported by at least by two frames.
Straps were used to keep the new planks in place as well as to pull them together to make sure that good glue connections would form between the new planks and the old planks.
Planks were as well screwed against the frames for the correct position, screws will be removed in a later stage to be replaced with rivets and final bronze screws were required.
Update January 14, 2011
Stern Renewal
After both sides were repaired with new wood and new frames inside it was decide to start with the stern.
During the first inspection the stern did not showed the actual condition where it was really in.
During the summer months and during the repairs of the aft side it showed that most of the inside wood of the stern was rotten away and not only on the corners where the sides do meet the stern.
Going over several web sides it shows that this is a common fact in most of the Storebro 34 built most likely due to the construction and the way water runs of the ship.
First all hardware was stripped of the stern the next step was to document all needed holes in the stern and positions of other removed hardware from which a drawing has been made.
During the removal of the aft cabin it was also noticed that the deck supports had been rotten away and it was decided also to replace these.
To prevent that the hull form would be jeopardized by removing the deck supports and the complete stern first new deck supports were made.
Pine was used and to get the same roundness of the aft deck as original the new deck supports were laminated from pine cut planks and glued together wile strapped from portside to starboard side over the original deck.
When the new deck support was finished the deck end old deck supports were removed.
When removing the stern in small sections and not to loose the hull form the new installed corner aft frames where connected with straps to the center aft frame to keep them in place.
Some minor wood repair had to be done to the 3 frames from the stern ad the point where they meet the deck.
After these repairs the new deck support was glued and screwed in place before the complete stern was removed.
The next step was after cleaning all the old wood and making sure it was dry to install first two layers of Okumee sheets of 4 mm and 6 mm thick to create a new base with the correct stern form for the mahogany planks to be placed on.
The okumee sheets were place over each other to cover joints between the different installed parts and to make the base as smooth as possible for the installation of the mahogany planks.
The two different sheets were 100 % glued with epoxy glue to each other.
After sanding the fitting started of the 20 mm thick mahogany planks which do have a tongue and groove which is better than the original installed planks.
One should be careful not cutting the planks to short since the roundness of the stern does have an influence on the length of the plank
After the first fit and pre-drilling the planks for fastening with bronze screws planks were removed again.
All new planks have been glued with colored epoxy glue to the okumee plates.
Plugs were glued in and than starts the slow process of cleaning the wood from the xcess of epoxy although most had been removed during the installation of the planks.
One important part is to use a band sander and not a rotating sander since one always starts with course and the groves created by a course sander will not be easy to be removed when these are circles on the wood.
Therefore the choice was made to use a band type sander which needs to be moved in the length of the planks in this case horizontal.
After the sanding a thin layer of epoxy was placed over the wood to protect the wood against the nature of the coming winter.
Update February 2 2011 Aft side deck repairs.
The Aft Sides
This short description tells you how we have handled the sides next to the deck house of the aft cabin.
Since the same problems exists on both sides only one side, port, will be described how changes were made.
First step was to remove all hardware and document the position of all hardware on the deck.
Next step was to remove the toe rail of the deck, this all was done by removing the plugs where needed and removing the screws to minimize the damage to the original construction.
Following the removing of the hardware was to remove the bottom plank of the aft cabin which rests on top of the deck, also in this case the plugs were removed and screws removed were possible in case it was not possible to remove the screw carefully the head of the screw was drilled of the shank this way it was possible to slide the plank over the original screw.
Before the bottom plank was removed the windows and window construction were taken out.
Since the windows are placed in a unknown compound it was difficult to remove them but with the help of an electrical heat gun the compound became soft and the windows could be cut loose from the wood.
With all above removed it was possible to remove the teak deck in small pieces. This was done till from aft till the forward cabin,
After removing the teak deck, which will be replaced due to the bad condition, earlier repairs were revealed which shows that materials were used which are common in shore side construction but not in ships construction.
That the news ones would be in the same position a temporarily support frame was built under both beams and fixed to the hull frames.
The new blank wood in the next picture shows the temporary supports installed under the rotten deck beams.
Both deck support beams were than removed and new ones were made from pine.
The new beams were placed on the support frame and fixed in position.
To make sure that the construction of the new beams will support the deck and hull the inner was kept longer than the outer this to prevent that on the same position of the ship a weld was made of both beams which could weaken the ships construction.
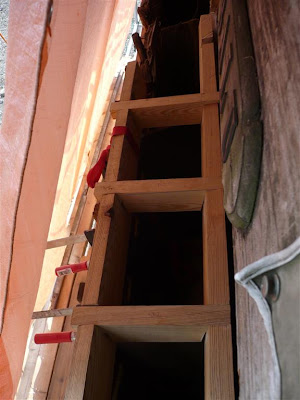
The next step will be the construction of the teak deck which is planned for late 2011.
Update March 14 Removing and Installing Rivets
The hull is riveted to the oak frames as well as on certain locations bronze screws are placed to hold the planks in place I presume during the actual placing of rivets.
Since the hull is flush, rivets are not shown on the outside of the hull; it has to be determining where the rivets are positioned in the hull.
Since the positions of the frames are know the paint is removed with a sharp scraper and hot air gun on the positions of the expected rivets.
This is an easy process which does not take to much time but make sure that all the paint is taken away so that the plugs visible.
In case of the Storebro wooden plugs can be located now after the paint removal, under the wooden plugs the rivets are fixed.
The good thing of the Storebro original built is that the wooden plugs are not glued into the planks and are easily coming out.
The easiest method I found was to use a small chisel to knock the plug out; one does not have to be to careful since the planks where the plugs are removed from will be replaced eventually.
The next step is to remove the actual rivet, going over the internet it is often mentioned to use a small angle grinder and cut the burrs of the actual rivet from the inside.
I have tried this but found out rather quickly that this is not an easy method for a wooden boat since damages to the oak frames occur rather easy.
Also on a lot of places the angle grinder can not reach the burr of the rivet.
Therefore I was looking for a different method in removing the rivets.
The easiest method I have found till so far is to drill the head off the rivets from the outside to the inside, when the head was removed the rest of the rivet was than punched out to the inside of the boat. The head of the rivets were drilled off, actually this is quite simple with a sharp new drill bit, and copper is a soft material. If you do not want to use directly a drill bit slightly larger than the shank of the rivet you can first drill a small pilot hole with a small drill bit followed by a bigger seize drill to remove the complete head.
Also in this case one does not have to worry that the wood is damaged since the plank will be renewed.
Then the rivet can be knocked out with the burr to the inside of the boat.
After the new planks have been glued in place and fixed with a screw the new rivets could be installed.
To prevent that the frames become a Swiss cheese the planks were drilled from inside to outside on the position of the old rivet.
The next step was to prepare the hole for the plug which covers the actual rivet.
This was done with a taper point drill which is of a set with a matching wood plug cutter.
After that the rivet was punched into the hole one has to do this carefully since the rivet is from copper and when one wants to make this a fast job there is a big chance that the rivet will bend in the hole.
For the next step you need a good friend or a neighbor who also loves wooden boats, I my case I’m blessed with all three a friend who is my neighbor and he loves wooden boats.
This since the next step the actual riveting is not that easy especially with rivet heads which are sunk into the wood. The rivet head on the outside needs to be kept in place with a punch and hammer while from the inside the rove is placed over the nail with a rove punch.
Nail is than cut to the desired length and than with a hammer rounded over the rove while from the outside pressure is placed on the nail head to prevent that the nail is pushed back through the hole.
Additional information can be found on the below web side.
http://www.faeringdesigninc.com/instruct.html
After all the rivets are in place the wooden plugs can be inserted in the holes.
Make sure that the grain of the plugs is in the same way as the grain of the planks.
In this case I glued the plug into the planks to make sure that they would not come out, boat will be out of the water for at least another year.
Next step is to remove the part of the plug which is sticking out of the plank this goes the easiest with a small sharp chisel. Sanding an in my case protecting the wood with several layers of linseed oil to protect the wood against rot.
Update April 3 2011 Winter time
This will be the last update for a few months since it is about time that I will start to continue the restoration.
Winter time is not the right time to work on the hull or any outer construction of the boat especially with the weather conditions of rain and snow and the cold temperatures which prevented me from using any type of glue.
One thing which needed to be done was the cleaning of the bottom not only in the cabins but also in the engine-room.
As with all older ships when one cleans the engine room bottom a lot is found which should have been removed in an earlier stage.
A clean oil free bilge is not only important for the environment but also in case of leakage or minor flooding of the boat one minimizes the risk that dirt will enter the bilge pump which can result in a failure of the bilge pump.
Due to the hatches in the steering cabin to the engine room the Engine room of the Storebro 34 is good to enter and one is able to clean almost the complete engine room bottom.
This process has been taken several weeks to clean and removing dirt and grease from the bottom is time consuming, also since I’m not as flexible as 20 years ago and it was freezing cold.
At the same time an inventory has been made from all overboard outlets and valves.
I was a bit amazed that a lot of overboard openings do not have a shut off valve although they are below the water line, while this type of boat has been designed for voyages across big lakes and coastal travel.
I will install on all overboard openings new valves.
Also I noticed that the engine cooling water inlet filters are placed below the water line which normally is not seen in small yachts.
Now that the bottom is cleaned a start was made with the removal of the paint, this is done for inspection of the hull from the inside as well as to apply linseed oil on the hull.
The same has been done with the aft cabin and after removal of the paint on the bottom two small area’s were discovered which will need some attention in the summer, wood is damaged.
This means removal of parts of the bottom planks and placing new inserts.
The cleaned area’s received several layers of linseed oil to protect the wood.
Electrical Installation:
This is another part where one can work on during the winter time it is important to get familiar with the electrical installation and layout in case situations arise which do need a quick follow up.
I have the impression that most of the electrical installation is still original and the projection at this moment is to leave the installation as it is with upgrades where required.
Since there are no drawings with the boat and since Storebro in
Sweden did not reply on my request for copies of electrical drawings I was more or left stuck with how all the fuses were connected to the electrical system.
Luckily I was supported by a Gentleman in
Germany from the Storebro club who has sent me pictures of the drawings which are clear enough to check the present installation.
As with all older projects over the years more wires are installed than sometimes really needed and not always in a proper and professional way.
I found a type of spaghetti in the fuse cabinet and around the batteries.
First thing was to determine which wires could be removed which had no use, this was not only the 12 volt circuits but also the 220 volt installed in the boat.
The next step was to shorten all wires which were to long and could be shortened.
The 220 volt circuit with outlets were checked and upgraded to ships standards although not finalized it gives me the necessary outlets on board the ship which allows me to plug in tools for the coming work inside and outside.
The drawings were checked against the installation on board and most of the fuses are still serving the circuits as per drawing.
Some changes had to be made to allow to new equipment to be connected and changes we made to connect original installed equipment on the correct way.
At this moment about 50% of the electrical installation has been checked and cleaned up.
Update August 19 2011
The Bow Replacement
Although I was aware that some of the hull planks under the deck connected to the bow needed replacement I was not really prepared to replace the complete bow, a so called nose job.
Earlier repairs had been done by removing planks of the hull which are connected to the deck and replace them with plywood due to rot.
The result was that, in my opinion a part of the strength of the construction was lost. Not only the hull planks were rotten away , but also the longitudinal deck beams running under decks were rotten and gone in several places. Especially where this beam is connected to the actual bow beam. Although new wood was added and rotten wood removed, I have the impression that the actual problem, water leakage from the deck down, was never addressed.
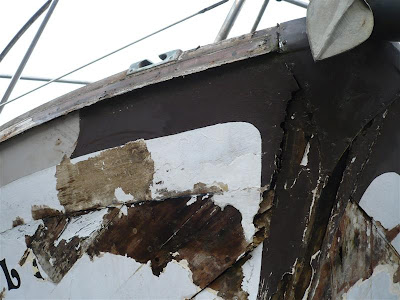
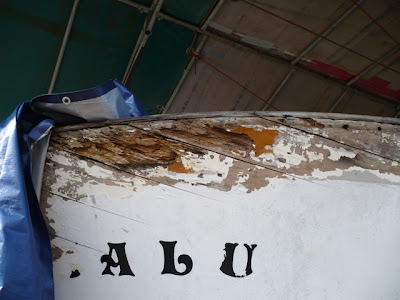
After removing all the rotten and bad wood from the hull as well as under decks of the actual bow the situation did not improve, more repairs were found, which in my opinion were not done professionally. The result of these further inspections resulted in that it was decided to remove the complete bow from deck to the keel. Although this is not a difficult job it has to be well thought through. Luckily I have my neighbor who helps me more than regular and who often thinks outside the box. His solution was simple: cut the complete bow out and just built a new one. So we did .
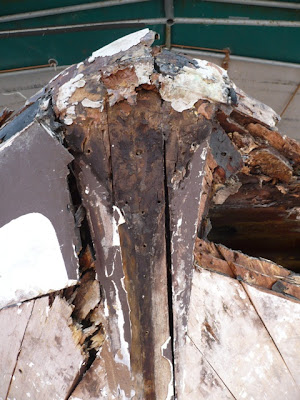
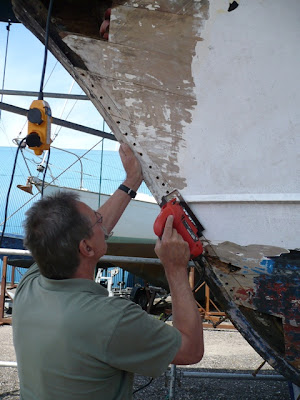
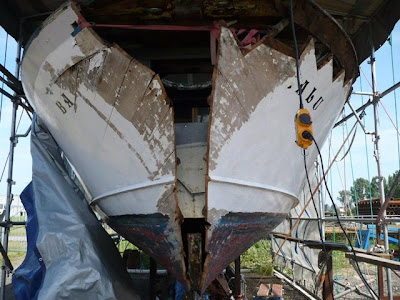
The actual bow beam consist of 3 pieces one center piece from top to bottom and two side pieces, these three pieces are hold together with long screws and threaded bolts. The next step was to find oak beams from which the new bow had to be built and shaped. To prevent a lot of cracking and distortion of the new bow I have bought old used oak which normally will not move or crack anymore. The next step is simple just copy paste the old on the new. To do this a lot of measurements were taken as well as shapes on different positions of the old beam which were transferred to the new beam.
When all measurement were transferred from the old bow beam to the new to be built bow the actual work started with cutting out the wood of a square beam and shaping this piece of wood into a new beam.
When the new beam was shaped and several times checked against the old one it was time to install the new beam, we must have done it right since the moment we placed the new beam against the ship it fitted exactly in the correct place no changes had to be made. The height was correct and even it ended up in the center of the deck. The beam was now placed in position with threaded bolts , connection between the inner bow beam and the new bow beam, and positioned at the top in the center of the deck and temporarily hold in this position with some screws.
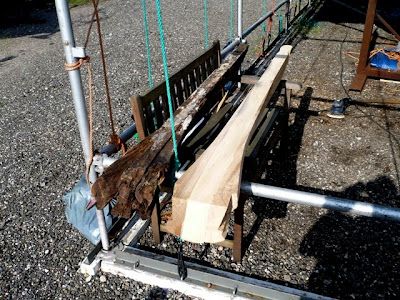
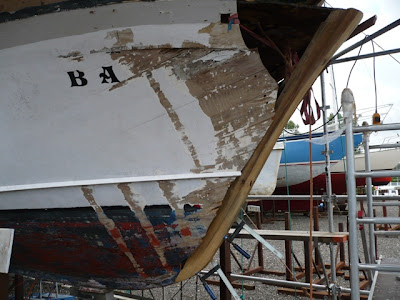
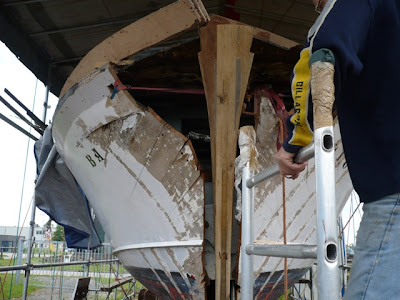
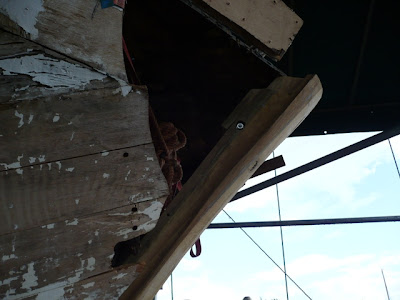
With the bow in place the next step was to install new hull planks, although this sounds simple it is far more difficult than replacing the hull planks from the aft side as was done in an earlier stage. The challenge is that the planks from the bow do have a different form than from the stern. They do not only bend from aft to forward but also bend from the keel to the deck as well as they are tapered from the stern to the bow. The first plank at the keel was not to difficult but the next one had to much torsion that after three attempts it was decided to make this piece out of a laminated piece of wood. From there on it was just placing plank after plank one left one right to keep the bow beam in place.
Than the point is reached where the last plank reaches the top of the bow, at this point the new longitudinal deck beams have to be installed before more bow planks can be inserted.
The Planks were screwed against the beam and glued/sealed with Sikaflex Glue and Seal, this to create a flexible seal between two different materials mahogany and oak. The planks were not glued with an epoxy glue or any other type of glue. This is the is done in the same way as original built.
The fabrication and installation of the replacement of the longitudinal deck beams will be another subject at the same time the finishing of the hull planks against the bow beam will be further explained.
Update October 2nd 2011
Replacement of the Longitudinal Deck Beams
The Deck beams running forward to aft under the deck and against the hull consist of two parts. The aft part till approximately the forward part of the deck house are made from Pine, the part of the deck beam running from the forward part of the deck house until the bow were made of laminated mahogany, thin strips, 10 mm, put together in the shape of the hull. The repairs/replacement of these laminated deck beams will be explained in the below text. As with all till so far found under decks wood these deck beams were rotten away and in some cases repairs was done which have not lasted that long even parts of the beams were missing near the bow. To make in our opinion a good repair both deck beams, portside and starboard side, were completely replaced. Instead of using mahogany planks it was decided to use marine plywood and of 9 mm thick, and glue these strips with epoxy together, this way creating a strong beams which at the same time , due to the epoxy, should remain water resistant. The choice for 9 mm thickness was made since these strips of wood can easily be bent in the correct shape required to fabricate new deck beams.
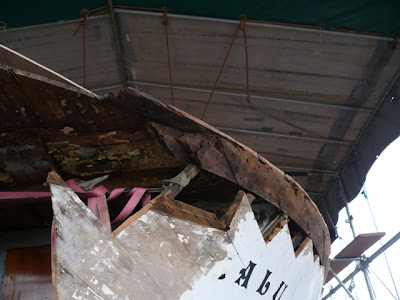
The first step was to remove the planks against the deck beam to find out how the original beam was constructed against the deck and against the hull.
The next step was to make a template of thick paper in the form of the too be built beam. This was done by placing the thick paper against the hull and then cut out the form of the too be built beam. After this paper model was finished a template was made of door skin, thin wood which was used as a template to cut the marine plywood which has been used to fabricate the beams. Although on the boat it looks like a straight line there is a curve in this beam as well as that the beam has a torque from aft to the bow.
Beams were made by placing the first strip of plywood against the hull to copy the roundness and bend of the bow. The next step was to glue each layer against each other. Every day one layer was installed to make sure that the epoxy glue had time to cure. Also it was needed to wait a day to remove the screws which were used to press each layer against the other one.
When the beams were finished, they were removed from the ship’s hull and the angle between the deck and the beam was transferred onto the new beam. Beams were temporary shaped with a sander, final shaping was done after the beams were installed and the actual deck beams were fitted between port and starboard, this subject will be explained in a later stage.
Old deck beams were removed from aft to forward and to prevent that the deck would fall down a support was placed on the actual deck beams running from port to starboard under-decks. This support is also needed for the correct position of the new deck beams under- decks.
After the deck beams were placed in the correct position, this is time consuming since a lot of measurements had to be taken to make sure that the deck beams are on the same height, ports side and starboard side above the keel. When we were satisfied with the new position of the longitudinal deck beams they were supported in place with some hull planks.
When they were fixed the rest of the bow planks could be finished, installing these last hull planks is also time consuming since the planks not only run from forward to aft but also from the keel to the deck, so there are two curves in the planks. After a few planks which took a long time to get a correct fit for several planks a paper template was made before the actual plank was cut and fitted in place.
The planks were screwed with brass screws against the new longitudinal deck beams and the frames. It was at the same time found that the most forward frames were rotten so new frames were made in place of the hull; this was done before the old frames were removed and before the old hull was removed. Since there is quite a bend in these frames they were laminated from oak and glued together with epoxy.
Eventually the new bow is finished, just left were some plugs to be installed when this picture was taken.
The following project is to replace the deck, deck beams between the bow and the deck house.
December 2011
Replacement of the deck of the bow.
After installing the longitudinal deck beams under the deck the complete deck of the bow needed as well to be replaced. This included all the deck supports, support for the escape hatch as well as other needed supports for deck equipment. This replacement will be done in two steps first step is to remove the old deck and replace the needed deck supports with a new marine 6 mm plywood deck.
Second step will be the installation of a new teak deck.
A start was made by removing a part of the deck, we did not want to remove the complete deck at once since the installed new longitudinal deck supports needed final shaping with the transversal deck beams. The first part of the deck which was removed was between the actual bow and the forward bulkhead, this included two deck supports.
By removing the complete deck not at once but in parts we could keep a reference between the old installed deck and the new to be installed deck. After installing the first deck supports we had a reference between the old deck and the new installed deck supports preventing that the new to be installed deck would be in a different position, higher or lower, than the original installed deck.
The new deck supports were made from pine and were shaped according the old removed supports, this was done one by one by more or less a copy paste of the old removed deck support. They were kept longer at the ends than the original ones and shaped to the correct length when installed. The reason that they were kept longer than the original ones has to do with the fact that also new longitudinal deck were installed which could be in a different position from each other compared to the removed ones. After temporarily installation of the deck supports it was checked if they were not installed to high, with the old deck still in place we were therefore able to check the correct height.
To have guidance for the installation of the new deck supports a small piece of wood was installed under the original deck supports before they were removed, see also the following picture.
This support was a guide for the installation of the new deck supports and was not removed until all new deck supports were fitted in place. The deck supports were fitted in the same way as original built under an angle in the longitudinal deck beams and screwed in place, the only difference to the original installation is that we glued them in place with epoxy as well.
The last deck supports which runs on the inside of the cabin from port to starboard side needed to be made before the actually new deck could be installed, since we do not want to remove the complete deckhouse yet. This was the one in the forward cabin which is round and which has the same curve as the rest of the deck from centerline to portside and starboard side to be able to let the water run of the deck. This round deck support was laminated from marine plywood strips which were glued together with two component epoxy. To get the same shape as the original one the old deck support was cut out in one piece as much as possible and the new strips of plywood were glued one by one against this old deck support to get the same curve and shape.
After all the deck supports were installed a check was made with strips of plywood to check if the roundness of the bow was correct, it was checked if none of the deck supports were higher or lower than the two next to it. After some minor changes and checking the complete deck supports from aft to forward it shows that all was installed as best as one could expect.
To make sure that ports side and starboard side deck beams are on the same height measurement were taken from one point of the center keel line to port and starboard, otherwise it can happen that one side of the ship is higher than the other side.
When all deck supports were fitted in their final position the support for the escape hatch was installed as well as the supports for the deck boulders. The support for the escape hatch was made from two layers of 10 mm marine plywood glued together and screwed in place on 3 deck beams. After installation it was shaped in the same curve as the deck beams where it is placed into. The actual hole for the escape hatch will be made after the teak is in place this will also result in that the deck support in the middle of the escape hatch will be cut out, this cannot be done at this moment since it provides strength for the installation of the to be installed teak deck. The supports for the deck boulders were made from oak as original.
The deck is made from 6 mm marine plywood like original, to make my life easier I have painted the inside deck white before it was installed, two layers of epoxy, the thin type with white pigment and one layer of normal white paint. This will have as a result that I have only to do some touch ups instead of painting the complete deck from inside which is time consuming. Also the deck supports have been sanded and put in a protective layer of epoxy. Before installing this prepared 6 mm under deck the white paint/epoxy has to be removed at the position where it will be glued onto the deck supports and longitudinal beams.
The new deck was glued with epoxy on the new deck supports and screwed temporary into the deck supports for good contact. The excess of glue was directly removed from the inside to avoid long and difficult work in a later stage by removing cured glue/epoxy. After the complete deck was installed the screw were removed, holes filled and the completed deck was placed in a thin layer of epoxy as a protection for the winter , the next step will be completing the complete marine plywood deck around the deck house before new teak can be installed. This will have to wait till next year, 2012, since the humidity and temperature prevents that epoxy glue can be used.
Some pictures of the inside
Before new deck
After the installation of the new deck
The hole for the escape hatch will be cut after the installation of the teak
April 2012
Replacement of the deck sides.
The only parts left before the new teak deck can be
installed are the sides of the deck next to the deck-house. The sides of the
actual deck are original installed before the deck-house was fitted. It is at this moment
not my intention to remove the complete deck-house since most of the wood of
the deckhouse is in a good condition. The complete teak with the sub-deck had
to be removed for installing a new teak deck.
First step was to remove all the plugs and
screws which hold down the teak deck on the transversal beams this to create as
less as possible damage to these beams which most are in a good condition in my
case. The next step was to cut with a Multi Tool through the deck where it
joins the deck-house.
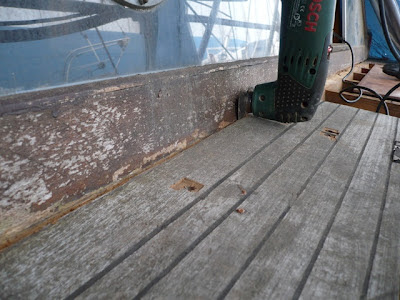
The deck was then
carefully removed from the transversal and longitudinal deck beams, the Teak
planks were hold in place with copper nails through the sub-deck into the
beams. After the deck was remove wood of the deck is still under the deck-house
which needs to be removed as well. With a small chisel and hammer this wood was
carefully removed, it showed during this process that the sub deck would not
move as well as that at certain points the teak plank would not give away.
Further inspection showed that at the point where the deck
house was placed on the teak deck that the teak planks were screwed in the
longitudinal deck beams as well as that the sub-deck was nailed into the deck
beams.
As one can understand
it is at this point impossible to remove the screws and nails therefore the
Multi tool was used again with a special saw blade for metal, the crews and
nails were cut between the beams and the sub-deck leaving behind a smooth
surface. The “groove “ where the sub-deck and the teak were fitted between the
beam and the deck-house were than cleaned properly from all rest pieces of wood
and the original kit used for water tightness.
After the deck was removed some more rotten wood was found
mainly at the point where the air intakes are positioned for the engine-room.
As can be seen from the pictures beams were rotten away as well as a part from
the wall between the cabin and steerage space, replacement of parts of this
wall will be described in a later stage.
New beams were installed in place of the air intakes and the
same time to prevent rot in the future this complete area was cleaned and
protected with 2 component thin epoxy, except of the hull of course which is
regular coated with linseed oil. Marine plywood, 6 mm like original was both
side coated with this 2 component epoxy to protect it against the weather. Before installing the sub deck at the position
of where it will be glued with 2 component epoxy onto the beams the sub-deck is
sanded to get a good bond.
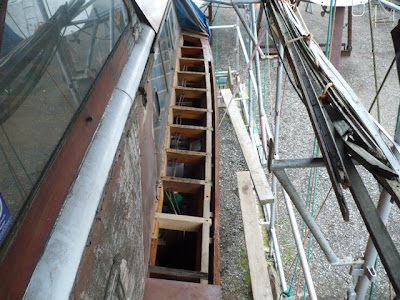
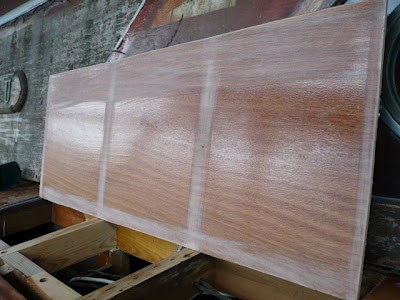
The new pieces of the sub deck are than glued onto the beams
and screwed down onto the beams, to make sure that a good bond would be created
as well as to prevent that holes would exist between the beams and the sub-deck
the amount of epoxy glue used was more than actually needed. This resulted of course
that on all sided epoxy would come out between the parts which were glued
together. This excessive amount of epoxy was removed before hardened and reused
to close the holes from the screw of earlier installed pieces of the sub-deck.
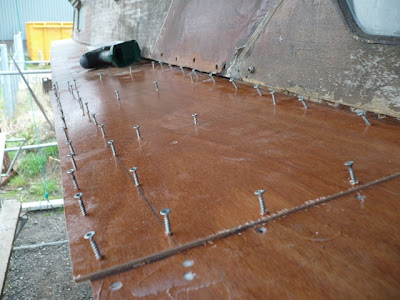
After 24 hours the glue had cured and the screws were
removed, screw holes filled with a thin epoxy to make sure that not holes would
remain in the sub-deck which could result in the future water ingress. When the
complete deck was installed it was sanded with a course sand paper grid 80 to
remove the high spots where wood was glued against each other as well as the
rest of the sub-deck. Than a new layer of thin 2 component epoxy was rolled over
the complete deck since during the sanding on several placed the original epoxy
was removed due to the sanding.
The next step will be installing of the teak deck which will
be another addition to this blog.
May 2012 Preparation for Teak Deck Installation
Due to the removal of the original teak deck between the sub deck and the deck house a gap remained.
This gap needed to be closed before the actual installation of the teak deck could be started.
There were two options discussed to close the gap, one was to fabricate a teak plank which would be slide under the deck house and at the same time would be a “guide” plank where the teak deck planks would be fitted against, the challenge here was that the gap was bigger than the new to be installed teak plank 12 mm compared to the original 16 mm. Second option was to fill the gap between the new sub deck and the deck house with a mahogany filling plank.
The last option was chosen.
Since there is some damage to the deck due to the removal of the teak planks it was decided to place a slightly thicker filling plank than the actual width of the gap.
First step was to fabricate a filling plank bearing in mind that the gap was around 16 mm, original thickness of the teak it was decided to make the filing plank 19 mm thick, this way approximately 4 mm was removed from the bottom side of the deck house, 1 mm for the thickness of the multi tool saw-blade.
Since there is an angle between the deck house and the actual deck, angle measurements were taken before the actual filling plank was made, bearing in mind that the filling plank should make a 90 degree angle with the sub deck.
With the filling plank prepared approximately 3 mm was cut from the bottom side of the deck house with the multi tool, using as a guide the to be installed filling plank.
In my case also the inside support planks between the deck house and the actual deck
beams were mainly rotten away and it was decided to completely renew these planks as well.
When these planks are removed the deck house is more or less loose from the actual deck construction and can move downwards and outwards. This might result in that when the filling planks are glued in position that the deck house will not be in the original position anymore. Therefore several temporarily supports were installed between the deck beams and the deck house. After these supports were insalled the complete plank was removed.
The new filling plank was fitted and glued in place with two component epoxy glue with an added mahogany pigment to match the color of the wood installed
To make sure that the glue line would be minimal pegs were installed to push the filling plank against the original deck house. Also the filling plank was installed in such a way that it slightly was sticking out of the deck house.
After curing of the glue the filling plank was sanded smooth with the deck house in the same angle as the deck house, this means a small part was removed from the filling plank at the top, but not at the bottom.
The reason that the bottom should not be sanded is that the bottom side of the filling plank should be with a 90 degree angle with the sub deck for proper installation of the new teak deck as can be seen from below picture
When everything was sanded and protected with linseed oil the result is more than satisfying in my opinion, also the next picture shows the teak plank in front of the filling plank under the deck house.
A new plank between the deck house and the deck beam was installed inside and plugs which was fixed in place with news screws and plugs.
July 2012 Preparation for Teak Deck
Installation Part II
It was noticed before the installation of the actual teak
deck could start that there were a few pieces of wood of the forward cabin aft
cabin and the steering hut had rotten wood where it is connected to the deck.
The main challenges were port side from the front cabin
window to the aft side of the aft cabin, starboard side front part of where the
side window meets the front window and a small part starboard side aft cabin
corner of the window.
On portside instead of replacing small parts of the wood it was decided to remove complete the first plank of the deck house from the front cabin aft window to the end of the aft cabin port side.
Before the plank was removed supports were place inside of
the cabin to keep the deck house in the same and correct position, it is important
to spent quite some time installing these supports otherwise the windows will
not close properly anymore.
The new to be installed plank was then placed in position, 5
meter/ 15 foot long although one would expect that this would be a straight
forward installation it took quite a long time to get the plank fitted
properly.
The reason for this is that not only the deck is placed in
an angle compared to the deck house but also the deck is not completely plat
over 5 meter length and runs in a small curve.
When all fitted well and the plank was in place the position
of the aft cabin windows was marked on the plank, plank removed again and the
necessary wood was cut out.
The next step was to fabricate the vertical aft window frame,
and connect this to the horizontal lower window plank, new, and the horizontal
top window frame old and still in place.
Same challenges with this piece of wood the horizontal plank
should be properly fitted in place due to the angle between the deck and the
deck house.
Original construction was used for installing this piece of
window frame vertical window part had two wooden pegs with fitted in the
original top window frame and in the new bottom window frame.
First the wooden pegs were cut out of the extra wood of the
vertical window frame next step was to cut out a hole in the horizontal new
window frame, first small holes were drilled next step larger holes were
drilled and then the rest of the wood was removed with a chisel and hammer till
all fitted correctly.
Than the complete plank was glued with colored epoxy glue in
place while at the same time the vertical window frame was glued in place as
well. This needed to be done otherwise it is impossible to get this vertical
window frame fitted.
To make sure that the still installed plank of the deck
house would like up with the new to be installed plank wooden pegs were
installed in a groove in both planks.
These grooves were made with a specific tool designed for these
purpose unfortunately I forgot to make pictures of this type of installation. On
the inside of the cabin the new plank was kept in place with small blocks of
wood screwed to the new plank and to the deck support beam, both should line
up.
With the new plank fitted the actual window frame needed to
be worked on to be able to fit the actual windows.
Window frame were kept smaller than actually needed, few mm
and sanded down to the correct seize to be able to fit the windows.
First the windows were placed in front of the wood, markings
were made windows removed and with a router the actual groove was made to fit
the actual window in place.
When everything fitted correctly the window frame groove was
coated with thin epoxy to protect the wood from water for the future.
Last picture shows the finished installation of the window
frame with the plank screwed in place to the inside beams and holed plugged.
Next larger window frame repair was the starboard side front
cabin window frame.
Portside window frame in the same position is still in good
condition.
As can be seen from the following pictures there is quite an
amount of rotten wood on both horizontal and vertical frames.
The window frame was cut away until good solid wood was
found and a new frame was made.
The vertical window frame from the front windows will be
replaced in a later stage but was needed to get the correct angle of
installation of the vertical window frame of the side window.
Since the window frame of the transversal front windows was
disconnected from the deck it had moved slightly in the direction of the aft
ship. As can be seen from the next picture the front window moved in the aft
ship direction after removal of the vertical side window frame.
This had as a result that the first vertical window frame
although fitted well did not look very good it was tapered. Also due to the
rotten wood it was not possible to take good measurements of the removed wood.
In short a new part of the window frame was made and
installed in the same way as the aft vertical window frame was fabricated.
As can be seen from some of the last pictures some teak has
been installed.
The teak deck installation will be the next blog when the
complete teak deck installation is finished.
Unfortunately at this time the weather is not in favor for
completing the installation of the teak deck lots of rainy days
September 2012
Teak Deck Installation
After the sub deck was finished and before the teak deck was installed all holes in the deck were filled with 2 component epoxy filler .
Afterwards the complete deck was rolled in a thin layer of epoxy to make sure that there were no gaps between the different installed area’s where teak will be glued on, for example between the deck house and the sub deck..
After the curing time the complete deck was lightly sanded to create a good surface for bonding the teak planks onto the deck with bedding compound.
The first teak planks to be installed are the ones onto the side of the boat longer pieces for the straight side and shorter pieces were cut to seize for mainly the bow. Keeping in mind that portside and starboard side should looks the same, planks were shaped in the same length from a wider plank and installed without tension.
The planks were temperately screwed down into position and shaped with the sides of the boat. The planks of the complete bow were kept wider than actually required this gives the opportunity to shape them with the side of the bow as well as after final installation to make them the correct width with a router following the side and removing wood on the inside of the plank till the sub deck, groove of the teak plank will be discussed in a later stage. Next picture shows the left side of the bow shaped while the right side is still needs to be shaped. The way the teak pank and the bow are shaped is that a falt almost vertical surface is created to place in alater stage a teak plank for side protection.
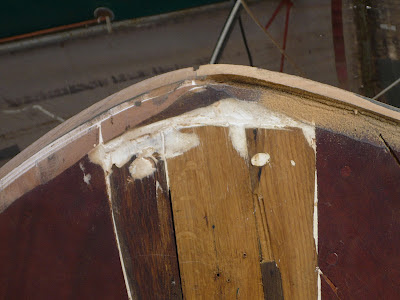
When all was correct the side planks were cleaned-degreased coated with a primer and glued down with Sika flex bedding compound. I have used Sikaflex and have followed the exact procedures as can be found on their web side, there are of course other bedding compounds and caulking systems on the market which are suitable as well.
The next step was to clean the excess of bedding compound at the inside of the planks and than figuring out the layout of the new teak deck onto the sub deck, this takes time to came up with an acceptable layout, by placing the planks loose onto the deck. I have tried to follow the original lines of the teak deck and this cannot always be followed due to the wider teak planks which are now on the marked 48 mm almost 2``.
When the layout was decided the planks were cut to the correct length and temperately mounted down with block of wood and clamps. I made small blocks of wood which were screwed down into the deck beams holding the teak planks in place during the dry fitting and during the actual gluing down onto the deck.
The holes were filed with bedding compound.
As can be seen from the nextt picture due to the groove in the teak plank it is possible to push the plank against the next plank and at the same time holding it down into position this methos was mainly used for the side panks since they are placed under a little tension to able to following the curve of the boat.
The next step was how to finish the teak against the deck house, original built the teak deck was installed and during a later stage the deck house was placed on top of the teak deck. Since I changed the construction the deck house runs now completely till the sub deck the teak will be placed against the deck house. There are two solutions one is to continue from the outside to the inside and make the last teak plank finish against the deck house and make it fit or place a teak plank from the same width against the deck house and fit the plank next to this plank and shape it in position. This is in my opinion the best and most nice way to do it. Although the teak experts will tell us to start installing the teak deck at the deck house and finish at the side it is the first time I installed a teak deck and I thought this was the best and easiest way to do it.
The next step was to shape the finishing planks in place bear in mind that I made the mistake to shape a long plank. When a long plank is bend after it is shaped it can not bend well and start to twist which will result that it will not fit properly, therefore I made sure that the finidhing plank was fitted with the minimum tension in place. This took a lot of measurements and time for fitting and shaping. It is important that I took the time to do this since I otherwise might have ended up with wider grooves between the planks which will not look nice after the deck is caulked and sanded.
When the planks were shaped to my satisfaction they were glued in place with bedding compound clamped where required and hold in position with wooden blocks. I noticed that it is important to have no gap between the planks during gluing down otherwise the bedding compound will fill up the groove between the planks and it is a lot of work removing it in a later stage with the chance of damaging the teak planks. Planks were hold also into position and pushed into the bedding compound with sand bags. No more than two maximum 3 planks were glued down at the same time. First were the two sides finished onto the sub deck.
Next part to be glued in place was the stern deck which was done in two times since it were short plank without any tension to be able to keep into position, also here were block sued and sand bags.
The stern was done after the sides were finished to get a good contact between the side planks and to make sure that the caulking lines would be followed. If one starts firts with the stern deck it will be difficult to match the side decks a small change in the angle between the stern planks and the side deck will result in a tapered gap between the stern deck and the side decks creating a strange caulking line. Therefore I started with the side decks.
Than came the deck of the bow, actually it was a bit easier since the planks can be glued down without any tension compared to some tension in the teak planks of the sides. First thing which was done was to decide the centerline of the deck and the width of the king plank . The sides planks in place more or less decide the layout of the teak planks from the bow deck, angle where the side planks come onto the bow deck. It was than installing one plank at the time port side starboard side and measuring their end position against the side plank to make sure that from the centerline the planks on both sides end up on the same position, If this is not done correctly the planks which end up against the king plank left and right will not match up which will be visible and will not look nice. In my case the planks almost lined up correctly left and right of the king plank with only a few mm difference.
The following step was to glue the teak planks down in position same plan was followed few planks ports side few planks starboard side hold in position by wooden blocks screwed into the deck beams and hold down by sand bags.
When the complete deck was glued down and time for curing the bedding compound was taken in consideration the grooves between the planks were cleaned The groove between the side plank and the teaks panks ending at the side plank were made with a router smaller than the width of the actual groove, a 4 mm router was used for a 6 mm groove. The router followed the side of the ship so creating a groove in line with the side of the ship. A 4 mm router was used this gives some flexibility with cleaning the extra bedding compund between the planks without having the chance to damaging the wood. Only disadvantage is that twice the router needs to be adjusted for the correct width of the groove which is eventually 6 mm.
Another method was also used for cleaning the grooves from the excess of bedding compound and creating the correct width of the groove where required, for example the shaped planks. A straight router was mounted on a base plate with two half round bolts which were out of line with the actual tool bid the two half round bolts gave the opportunity to guide the router through the grooves without removing any wood just removing the excess of the bedding compound while following the groove to be cleaned.
Since there were some of the grooves not pre-cut the same principle was used for cutting a new groove between the planks. It was made sure that one of the two planks has the original groove which is a part of the plank for guidance of cutting the correct width of the required groove between the two planks. The following picture shows a partly cut groove between two planks as can be seen the original groove is on the plank placed against the deck house which was followed with the router to create the complete groove between the planks.
When all grooves were cleaned and cut were required the complete deck was vacuumed and grooves checked for their cleanliness, it showed that also that the new teak deck was almost the same as the original installed teak deck.
When all the grooves were degreases and prepared for the deck caulking in one day the complete deck was caulked, bearing in mind to push the caulking into the grooves with a flat knife and leaving an excess of caulking sticking above the planks. Other method is to tape next to each groove before the caulking is applied which in my opinion creates a lot of extra work especially since the complete teak deck needs to be sanded and the excessive caulking will be sanded away. It was made sure that where grooves ended against the hull that tape was placed to prevent caulking running out between the grooves.
A finished deck with caulking does not look very appealing but when sanded it will look great in my opinion.
After a period of two weeks caulking needed to be placed between the teak deck and the deck house although enough bedding compound was used when installing the teak planks against the deck housebedding compound was pushed out between the teak planks and the deck house. An extra filler needed to be placed between those two surfaces in my opinion. Before this filler could be placed the teak planks next to the deck house needed to be sanded when this was done all was degreased and tape was placed for applying the caulking. Directly after the caulking was finished the tape was removed and the caulking left to dry.
The aft deck was completely sanded for the installation of new window frames the same was done with the bow deck but only in the position of the new window frame. During this sanding it showed that a few air bubbles were entrapped into the caulking resulting into holes these holes were cut out degreased and filled again with caulking, in this case tape was used to make sure that no caulking would end up onto the sanded deck. Sanding again caulking from the teak planks might result inlower spots on the teak deck which can result in places were water will collect.
The old window frame was placed onto the teak deck of the bow and the good part was that it fitted without any major gaps, only thing left is now to sand completely the teak deck but that will be done in later stage since more work needs to be done at the deck house, new window frames of the bow and stern windows, which will be the next blog.
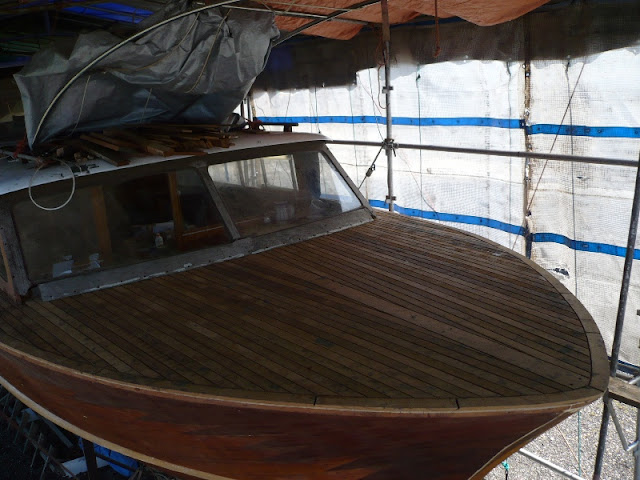
Replacement bottom window frame aft and forward
The bottom part which rests on the teak deck of the forward cabin window and the aft cabin window were rotten away and cracked.
These window frames needed to be replaced as well.
The first one which was done was the aft window frame since it had the less roundness onto the deck and a less round curve as the front window. More or less this was a practice frame for the more difficult frame of the front cabin window frame.
The window frame is made from 2 pieces of 12 mm thick mahogany planks which are roughly shaped and glued together with colored epoxy and placed on a jig which had a larger curve than the actual window frame required.
After the glue had cured and the clamps were loosened it showed that the new made plank had a curve which was less than when the plank was clamped onto the jig.
The next step was to shape the plank in the form of the aft deck and with an angle to make a good contact with the teak deck.
For checking the new plank/frame it was clamped onto the top frame with supports.
One can than check if the angle of the bottom is correct as well as that the new frame follows the actual curve of the deck. Next picture is taken during the shaping of the frame.
This shaping is timely since the deck is curved and the frame needs to rest completely on the deck in the correct angle. When preparing and gluing together the bottom frame it is made over-sized due to the fact that during the shaping the frame increasingly gets smaller and when the old frame is exactly copied one will end up with a to small bottom frame to fit the windows.
When the bottom frame was shaped to the deck curve and with the correct angle it was time to start with the renewal of the sides and the center part of the window frame to complete window frame renewal, except of the top part which is still in a good condition.
The above picture also shows the over sized bottom frame while test fitting the actual window in position. This extra wood is in a later stage removed after the window frames were glued in place.
When all was dry fitted correctly the side, center piece and the bottom part of the window frame were glued together with colored epoxy glue.
The next step was to glue the window frame with sides and center piece into place.
The complete unit was screwed onto the deck as well as onto the sides of the ship. The center piece was installed as original with a pin into the hole of the top window frame.
The bottom window frame was also screwed from the inside onto the deck.
The bottom frame was not glued with epoxy onto the deck but with double sided marine flexible tape.
Deck was degreased to remove the natural oil of the teak deck.
To hold the complete frame in place and fix it straight onto the old still in place window top frame clamps were used with blocks which were covered with duct tape, Epoxy will not stick to duct tape.
Left over epoxy glue was used to insert the wooden plugs at the same time.
When all was dry the whole area was sanded and the sides shaped in round corners as original.
The actual glass windows were fitted in the top window frame and the bottom window frame and the sides were shaped to the correct seize. After that the actual groove where the window is placed into the frame was made with a router.
The next project was to renew the bottom window frame of the front cabin.
First attempt failed since the curve used for this window frame was not enough, the glued planks when the clamps were removed and the tension was taken off them came back to almost a straight plank. I used a curve of +/- 3 cm in the middle and this was not enough.
The second attempt I made was with a curve of +/- 6 cm in the middle deeper than the original removed bottom frame and the new bottom frame came out almost perfect. The jig used is not that professional but it served its purpose.
The next step was as described for the aft window frame to shape the frame to perfection and to follow the curve of the deck and the correct angle between the window frame and the deck.
When that was done also here the sides and center piece of the window frames needed to be replaced.
Than the following step was dry fitting the window frame parts together on the top of the teak deck,and against the sides of the deck house this was done with the bottom piece center piece and side pieces.
The bottom fame was screwed against a small support which by itself was screwed and glued onto the teak deck like original. You can see this support on below picture which was made of two pieces of mahogany glued together and shaped in the roundness of the window fame and shaped into the same angle as the window frame is placed onto the deck.
When all was shaped to acceptance all was glued together in place, bear in mind that during the dry fitting screws were installed to make sure that when all would be glued in place it was done correctly,
The same double sided tape was used between the bottom frame and the teak deck.
After installing the plugs the whole area was shaped, actual windows were fitted in the window frame and all was sanded.
During the sanding I noticed that I minor mistake was made with inserting the screws between the side frames and the side of the deck housing, a few of the screw heads showed through the wood. Most likely this is a result off drilling to close to the edge of the wood and not deep enough into the wood.
Since I was not happy with this fact the wooden plugs were removed again and the screw removed, although this sounds simple it was not the case.
The screw was inserted when the two parts were glued together with epoxy resulting that the screw was fitted in the wood with epoxy and could not be removed easily.
So what I did was to drill a small hole in the center of the screw, making sure that most of the groove of the screw head remained in place and then removed the screw.
By drilling a hole in the bronze screw the screw gets hot/warm resulting in that the epoxy “melts” one can than remove the screw reasonably easy.
New hole was drilled new screw inserted and the whole was plugged and sanded again
Repairs Steering Cabin
The next step in replacing rotten wood was the upper plank of both sides of the steering cabin. These planks are fitted under the polyester covering on which the window frames is placed of the steering cabin.
The main reason in my opinion for the rotting of the wood to be started is that where two pieces of the polyester are meeting no proper seal was installed or has been disappeared over the years. This resulted that water could ingress between the polyester part and the wood not only resulting in that the upper plank was rotten away but also resulting in rotten wood on the inside of the forward cabin and the wet cell. Earlier repairs were made with looks like polyester but the root course was not attended according to me, the gap between both polyester parts.
The plank was removed until the original connection with the other side plank. Rotten support wood on the inside of the removed plank, which supports the window frames, was removed as well. From the inside the window frame was supported to make sure that when the plank was removed the position remained the same thus preventing that after the repairs the window still could be opened.
New wood was glued in place with colored epoxy and kept in place with supports from the inside with wooden blocks. The new plank was shaped in such a way that the angle was the same as the original plank. This to prevent that in future water ingress can happen.
The plank was than screwed in place as original onto the window frame support beams, holes were plugged. To make sure that the plank is protected from water ingress a large amount of epoxy was inserted into the space between the polyester and the inside support beams, more or less the not visible part of the plank is embedded into epoxy.
After both sides were in place all was sanded at the same time all old screw holes in the sides were drilled out and filled with plugs. The reason for this is that the wood showed a start of rot on the positions were screws were inserted and where screw holes poked through from the inside.
When both sides were sanded forward to aft port as well as starboard side the old sealant was removed between the polyester roof and sides. After cleaning and de-greasing new silicone seal was inserted in this opening. Painters tape was used and removed before the silicone dried.
Cracks between the two polyester parts were closed and glued together and both sides of the cabin were sanded again.
Instead of using varnish for protecting the wood I have used Owatrol Deks Olje D1 and D2. I have followed the instructions as can be found on the internet, it took 15 layers of D1 oil before the wood was saturated the next step was to apply the D2 oil which was another 6 layers.
Main reason for using Oil instead of varnish is that the D1 oil penetrated deeper into the wood than varnish and in my opinion protects the wood better from weather influences.
February 2013 Floor boards Cabins
Winter time is not a good time to work outside, the work done during the last summer 2012 and the autumn resulted in that the boat was more or less closed windows in place and all the decks in place again.
Boat was covered around the bow and aft cabin with tarp to protect the boat from water ingress, not through the deck but through the windows which were in place but not sealed yet.
During the installation of the teak on the deck more than several short pieces were left over as well as some full lengths, since I was not pleased with the original installed rubber mats on the floors of the cabins it was decided to install teak on the floor boards.
In between the teak planks is a gap of 6 mm which normally is filled with Sika flex black or white neither of them were appealing to me therefore I have filled the gap with wood strips made from European Ash ( Fraxinus Excelsior).
These strips were cut 6.2 mm X 6.5 mm from a beam. The reason for this seize is that it will fill the gap completely of 6 mm and the strip sticks out above the actual teak planks, with the idea that when the teak planks are glued onto the actual floor board that they are pushed into the glue for a tight fit.
With the teak planks installed on the floor boards instead of the rubber mats the distance between the floor and the ceiling will become less, this will be solved by removing wood with a router at the position of the supports under the floor board, thus regaining the original distance between the floor boards and the ceiling.
First step was to find out how much teak was actually needed and what could be done with the available teak.
It took some time and moving short pieces around to be able to cover all floor boards in the 3 cabins, not the steering cabin.
Second step was to remove the rubber from the plywood floorboards, this was not to simple since they were glued in place with contact cement.
After trying several methods tried , one of which heating the rubber in the hope that the glue would let loose or get soft I found that the best method was to place a thin piece of metal between the wood and the actual rubber math and so piece by piece separating both.
When the rubber removed from the wood glue residue was left and the only way to remove this was to scrape it off I have tried to sand it off with a sander, different types as well as heat but found that the best method was to just scrape the glue.
Than the wood was sanded and all paint and glue residue were removed this is needed to get a good contact between the glue and the wooden floor and teak planks.
Right side of the picture is sanded left side after scraping.
Next was the actually teak plank installation on the wood floor panels.
First were the sides of the teak cut to seize this was done while the floor board was in place, I found that the original floor boards were not always cut to the exact space available on the floor and therefore some adjustments were made with the teak sides where in between the teak planks were placed.
I have tried two methods for installing the teak on top of the floor boards one was to install the 3 sides first and glue them in place, next step was to install the teak planks in between the 3 sides and glue them in place at the same time fitting the 4th side of the floor board. The next day the wooden Ash strips would be fitted in between the teak planks. I found that this was very difficult mainly due to the fact that not all grooves were the same width sometimes a difference between ½ till 1 mm which made it almost impossible to get a good fit between the teak planks and the Ash strips.
Second method worked out much better.
First were the 4 sides of teak rims installed on top of the floor boards and glued in place.
Than the teak planks were cut to fit while at the same time the Ash strips were dry fitted between the teak planks. When all fitted to my satisfactory the planks and strips were marked to make sure that all was glued in the same position as dry fitted.
I have used two component epoxy glue mainly because the planks are short and will remain dry in contrary with deck planks. One can also use bedding compound of course.
As mentioned in the beginning the Ash strips were slightly wider and higher that the groove between tow teak planks when glued in place they were sticking out.
When now clamps are placed over the just installed teak planks the Ash strips are pushing the teak planks into the glue making sure that they will remain in place.
Before gluing the teak planks down one has to make sure that they are de-greased the same way as is done with deck teak planks. The wooden clamps are taped at the bottom with Duct tape to prevent that they will glue together with the teak planks.
When all is dried and after the first sanding it is possible, at least I experienced it that there are some minor gaps between the teak planks and the ash strips as well as at the end of the teak planks and the teak side strips. I have filled those with teak saw dust mixed with epoxy glue to remain in the same color after sanding.
Than sanding again and making sure that all is flat and sanded in the right grain.
I have used a band sander to remove the high spots only, which were the Ash strips. Than a rotary sander to make the surface as smooth and clean as possible and as last a flat square finishing sander which was used in the length of the teak planks so removing and scratches out of the wood as a result of the rotary sander.
The wood was than treated with Owatrol D1 oil in the first place to protect it for the rest of the winter and in the second place it is a natural oil for preserving the teak planks.
Also I think that maintenance in the future will be easier over varnished teak planks.
And I’m pleased with the result below picture of the two aft cabin floor boards.
Since the tight fit of the wooden floor boards with teak it was difficult to lift them not only due to weight increase. I did not want to drill round holes in them as original but installed a flush mount hatch ring.
Although this sound simple one has to start to drill and cut in the just finished teak planks and a mistake is easily made.
First is to decide where the hatch rings will need to be installed so that is visually nice as well as in an area where the floor board can be lifted easy.
I have used a hole saw to make the round hole for the actual ring house, and the rest of the wood was removed with various chisels. I made sure that last thing done was to cut the exact size of the rectangular hatch ring was cut out of the wood. This was done just before the fitting in place of the hatch ring.
As can be seen from the following pictures the result is in my opinion satisfactory, at least I do see this as an upgrade to the boat.
Picture of aft cabin original
Picture of the aft cabin with 3 floor boards in place two sanded and one in one layer of oil
Picture of aft cabin with finished floor boards in oil and with hatch rings.
Next picture shows the main cabin with the door which shows the difference between the original floor covering and the teak planks.
The last picture shows the main cabin with the front cabin with finished floor boards and installed hatch rings, one can see that the lines in the teak planks continue from the main cabin into the forward cabin.
What is left is the final installation of the teak planks under the table, left side of the picture, this will be done in a later stage since other work is planned in the same area and under the to be re-installed table.
May 2013 Keel Repairs
It looks like that the winter slowly is going over into spring, at least the temperatures at night are getting above 5° Celsius which means that I’m able to get some parts glued in.
One of the underwater ship projects left is the replacement of a part of the keel.
The most forward part of the keel where it meets the bow is split and looks rotten.
Although I have checked the inside and the wood of the inside part of the keel is sound and good.
First it was decided till how far the wood would be removed. Than the bolts which hold the inner keel against the outer keel were removed and it showed directly that water ingress had been around the threads of the bolts resulting in some rot in the wood.
When all hardware was removed the wood needed to be removed.
First attempt was with a plainer which did work but was not wide enough for removing all wood in one run at the time. The good news was that the wood was not as rotten as expected but just cracked.
Next attempt was with a tiger saw, reciprocating saw with a long saws blade.
Did worked well but as expected the cut line was not 100% straight.
After several hours working I was satisfied with the form of the removed wood by sanding and shaping the form to a more square form where the new wood would be fitted in.
The next step was that a template was made from a piece of scrap wood and fitted against the hull.
This form was than checked on both sides of the keel at the position of the removed wood and then drawn onto a piece of wood for the new to be shaped keel.
The new piece was shaped out a square beam of 150 X 150 mm.
During the fitting the new piece was regular fitted against the hull and in steps shaped to the best possible fitting.
One should take care during the fitting that the new keel will fit flat against the hull otherwise one will find large gaps on one side and a perfect fitting on the other which creates extra work or the chance that too much wood is removed from one side.
Therefore I used a support with kegs to fit the new piece as straight as possible against the actual bottom of the boat.
When I was satisfied with the fitting of the new piece especially where it meets the old keel under an angle the new piece was fitted with kegs against the hull in such a way that it was in the right position and as tight as possible against the hull.
It was than possible to drill the holes from inside out through the new keel for the threaded rods which fix the inside keel against the outside keel.
Nuts were tightened and another check was performed if the fit between new and old was satisfactory.
New keel was then removed and shaped for a better fit on the sides and bottom, it is easier to perform this task when the new keel is not mounted yet, but I made sure that at least 1mm on both sides would stick out for final sanding.
The new keel was removed, threaded rods as well.
Now the new keel was fitted with seal and glue from Sikaflex pretty large amount was used to make sure that no holes would be between the old and new wood, so at least 200 ml was forced out between the old and new keel but I was sure now that a 100% coverage of the kit was between old and new wood.
At the same time it was made sure that the threaded rods were covered with kit before they were pushed into the holes for the rod, this to make sure that a water tight seals would be created.
After drying of the kit, which took several days, the new keel was sanded in shape to fit the old keel, bow beam and hull.
To make sure that the shaping would be similar port side and starboard side the stainless steel rubbing stroke was fitted temporarily against the new keel. This way shaping was done by following the rubbing stroke.
After the final sanding was finished the wood was protected with linseed oil like the rest of the hull.
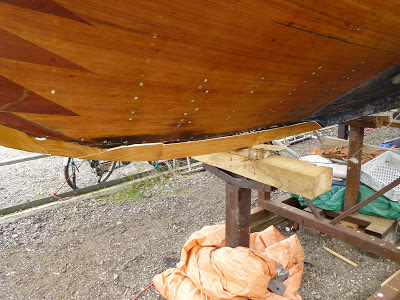
Main Cabin Repairs I
Aft Wall
The following part describes the repairs of the aft wall of the main cabin.
As earlier described due to the water ingress between the two GRP deck parts the aft wall of the main cabin, mainly port-side was rotten away.
Although the wall looked fine at the first inspection see below picture, after dismantling several components the condition of the wood was in a poor condition.
Taking the small locker apart showed where wood was rotten and where it needed to be replaced, not only the wall of the cabinet but also the wall between the main cabin and the steering cabin.
The wood of the cabinet was removed till the level of the bench so that when the new wood is installed no line would be visible between the old and new construction.
At the same time the wood of the wall which was rotten has been removed this gave also the opportunity to install the main heating supply to the main cabin and the forward cabin.
New marine plywood was installed in way of the removed wood, same thickness as the original wall.
The result is now that we have marine plywood next to mahogany veneer which will not be a nice result of finished repairs.
Since the original wall had a lot of holes it was decided to place a new 3 mm plywood wall with mahogany veneer over the existing wall.
First all varnish was removed of the present wall and all holes were plugged where required.
Wall was again sanded to get a smooth surface.
Unfortunately I was unable to remove the door frame of the cabinet and I decided to place the new wall covering around the door frame. The line between the two pieces will not be visible due to the cabinet.
A separate piece was placed inside the cabinet to cover the old and new wall as well to make it a uniform new wall.
The new panels were glued with contact cement against the existing wall and then varnished
After placing the new wall of the cabinet into place I noticed that the new marine plywood with mahogany veneer did not matched with the new wall.Not only different type of wood grain but also a complete different color.
It was then decided to also place on this part of the cabinet the same veneer as was placed onto the wall.
The veneer was placed in such a way that it looks like that the wood structure continues.
.
When all was fitted and glued in place the cabinet could be put totally together with new trim pieces on top as well as a new top onto the cabinet.
Holes of the screws were plugged
After everything was sanded again the whole area was varnished several times.
Window frames Steering Cabin
Last big project is to replace the wood of the steering cabin window frames.
All wood at the bottom side where it meets the GRP is rotten away or damaged by water ingress.
Holes can be seen for example where the front part meets the side parts.
The first part was to make the curved bottom window frame which was done the same way as earlier described for the main cabin bottom window frame.
Two 12 mm planks epoxy glued together in the correct shape.
This two glued planks were left for several months due to the winter strapped to the original window frame to prevent that the new glued planks would lose its curve.
When removing in a later stage the original plank it showed that the piece was made out of 4 pieces, thinner planks than I used which would have made it easier to get the correct curve. When fitting the new plank I had some trouble fitting it and getting the correct curve and roundness.
Since the windows were still in the frames and were difficult to remove and since I did not want to take the risk to damage them, crack them, it was decided to use the multi tool and cut the old frame loose from the actual glass of the window.
And in a later stage remove the kit/glue and rest pieces of wood of the actual glass.
During the cutting of the wood it became clear how bad the condition of the actual window frame was it fell apart into different pieces
When the bottom window frame was removed the support mounted on the deck remained in place, this part as expected was rotten as well.
The good thing is that this part is mounted from the top onto the GRP deck which runs from outside to inside, removing the wooden plugs gave me access to the screws.
To be able to shape the bottom forward window frame it is needed to install first the two support pieces onto the deck, which had to be made new as well.
First attempt was to shape them out of one piece careful measuring and shaping the new piece resulted that it did not fit, not even close. Even with further shaping the new piece did not even came close. This mainly due to the round curve which is under an angle as well as the roundness of the deck with a sharp kind of roundness at the edge of the window frame at both sides.
Second attempt was to laminate different layers of wood mahogany together thickness used was 10 mm. The planks of 10 mm were shaped into the same roundness and approximate angle of the support with the deck. The first two layers of wood were glued and screwed together onto the deck with blocks under the wood high in the middle and smaller blocks to the side this way compensating for the natural way of the wood, straight plank, when the tension would be released.
After the two first planks were set they were removed and a jig was made on another plank with higher blocks under the two first glued planks which were glued together to keep the correct curve.
The first two planks were screwed onto this jig at the points and then each day another plank was glued and crewed onto the earlier installed plank.
In between the the fitting of the planks screws were removed.
Not only the bottom part of the front windows was rotten away but also the bottom part of both side windows a screw driver could be pushed with ease through the wood.
Rotten wood was removed at one side to make sure that from the other side if required additional measurements could be taken to get the original shape back as original built, although difficult since from both sides on the same place the wood was rotten away.
From the side window the complete bottom piece was removed as well. It was not completely rotten away but in view of the difference in color which would show after repairs have been made with an insert it was decided to replace the complete bottom piece.
To make sure that the pen (pen and hole construction) of the aft part which runs from the top window frame to the bottom window frame remains intact the wood from the bottom window frame was cut away with a multi tool before the bottom window frame was removed. The extra wood was then removed from the actual pen so that when the new bottom piece would be installed the same strength would exist as before the repairs, pen and hole construction.
When the bottom piece was removed it was noticed that the support wood for the bottom window piece was also rotten at the front. Also this piece is mounted from the top onto the deck and was removed untill the point that solid wood was found.
When the wood was removed access was available between the two GRP pieces and the gap was cleaned out ,thickness of both parts reduced and the gap was closed with a glass fiber math and glass fiber two component epoxy.
New support piece made for the side window, not mounted to the deck yet since the plan is to paint the deck in way of the new window frames before these are mounted.
The wood is kept higher to be able after installation to sand it flush with the original still installed support plank for the bottom window frame.
The deck house is supported and measurements have been taken before all window frames were removed from the sides and the front, one side of the frame remained in place, port side, until repairs have been completed at starboard side and the front windows.
Next step was the sand the deck in the way where the new window supports would be fitted. Deck was sanded inside and outside, inside was pretty simple no new paint coats were used in the 40 years of service but outside at least 4 coats needed to be removed before the original GRP deck was reached.
At the same time the holes in the deck were closed as well some groves from old sanding of the deck with two component glass fiber epoxy.
When all was smooth the new front window frame supports were mounted onto the deck.
After the installation the angle was checked between the deck and to be installed new window frame, although carefully made the angle was too steep and the new window frame supports after mounting them onto the deck. They were sanded into the correct shape and the angle was checked regular.
The correct angle was taken from the removed pieces.
When the correct angle was reached both pieces were sanded to the correct height, as with all pieces like these I find it rather difficult to get them in the correct shape, therefore I make them over sized which gives me the opportunity to sand them to the correct dimensions.
When the angle was to my satisfaction the new window frame was temporary mounted against the new supports although it looked when holding the new frame in front of the new supports that the shaping was not even close, it showed that when the new frame was mounted against the supports that the frame was correctly shaped. What I learned is that new curved and round parts under an angle should be regular fitted and not only hold in place but actual mounted, with clamps for example, to make sure that not to much wood is sanded off on side while it might not even be required.
The deck , one side and front were sanded smooth high spots of the repairs removed and was coated with a two component white paint. At the points were the new window frames would be installed two coats were painted.
The next step was the fitting of the new parts onto the deck house, at starboard side one side frame at the bottom and one side frame at the front.
Although this looks not to difficult after all new parts were measured and copied as best as possible from the removed parts it came to me after more than one day fitting that this method might not have been the best approach.
Eventually all fitted to my satisfaction.
What I did regular during this fitting was to position the window glass on the front side frame to make sure that the angle of this part of the wood was in the correct angle.
This could be easily measured from the window to the edge of the wood this should be a straight line in parallel with the window glass.
When fitting the new front bottom window frame it not only took a long time to get the correct fit but I also noticed every time it looked like that the angle changed as well as that at a different point the wood needed to be sanded to get the correct fit.
The trick is the every time the frame is positioned for checking the fitting of the wood onto the deck that it needs to be clamped into position. One can than exactly see if the fitting onto the deck is acceptable.
When the fitting onto the deck in the center is correct and the new plank is not completely in position at the sides a gap will be seen at the sides.
At the same time a mark has to be made onto the plank and the deck to make sure that the position is every time the same. One can see in the second picture that when the new window frame is not clamped onto the support that the plank sticks out above the deck which gives the impression that the fitting is not correct.
All new parts where than removed again and the supports were sanded smooth and coated with two component epoxy to protect them against weather. The same with the inside window frames. Second step was to lightly sand the coats of epoxy and then coat the planks with two layers of varnish.
The inside side support which was rotten was removed and replaced by a new piece of wood, also this part was coated in epoxy to prevent future water ingress.
This part was also screwed from the top onto the deck.
New piece were visible inside was slightly sanded and coated in two layers of varnish.
The reason for all parts which are visible from the inside to varnish them is when they are installed that no painting is required which will also prevent that the new painted deck will have the chance of varnish stains.
The new part was screwed onto the deck and glued at the bottom with Sikaflex Seal and Glue to close any gaps and prevent water ingress.
For the other side it was decided first to make the new parts fit onto the old structure, this showed to be a major time saver, better fitting new onto old and replace them one at the time.
First part fabricated was the front side part of the front window.
Next step was to fit the new front side window frame with the first new piece.
Then the bottom window frame was removed and a new one fitted
.
As mentioned before this system worked quicker than the first side which I did with taking measurements removing all old wood and making new parts and then try to fit them together.
As the next picture shows it became like a 3 Dimensional puzzle.
Since I wanted to keep the boat the same as per original design and to be able to take the steering cabin off, I have been searching the web for a new rubber seal between the steering cabin and the deck house I have found one which is close to the original.
Same thickness as the original one only a round edge instead of a more or less straight one at the bottom.
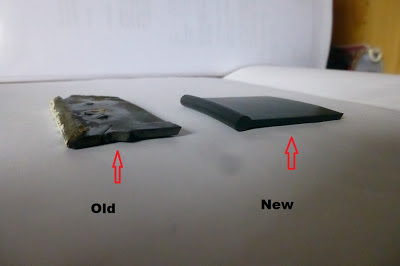
With the window frame removed it was now also rather easy to sand and varnish the steering console which normally is rather difficult to the limited space on the side and difficult to reach at the front side.
Next step after I was convinced that the fitting of the new wood pieces was correct to place the rubber onto the side planks which are placed onto the deck house. I used the same method as original and stapled the rubber onto the wood, bear in mind the wood where the rubber is mounted against is protected with two component epoxy.
Then one side was in my case ports side was mounted onto the deck and glued with colored two component epoxy in place , this was the complete side window frame. I used a very small amount of sikaflex between the support of this plank and the GRP of the deck house just in case when there is water ingress to prevent that it will enter the minor gap between the GRP of the deck house and the wood.
The next day the other side was installed and glued in place
The third day to front window frame was installed and glued in place.
This took quite some time the plank being slightly under tension and fitting it into the two side pieces.
The plank was screwed against the inside supports and clamped where required to get it exactly in place.
In a later stage the screws were removed and the original bolts and nuts were installed.
Next step the whole construction was sanded to remove the epoxy which came out between the different pieces.
After the sanding the actual glass windows were held in front of the new construction and the outer dimension of the glass was drawn onto the wood. Then a second line was made which was the height of the inside window frame 10 mm high.
The wood excess, more than 10 mm was now cut of with a small circular saw with laser point.
The next step is to follow the wood with a router of 10 mm to create the space where the actual window glass will fit in. As can be seen from the next picture this creates a lot of wood particles throughout the boat.
The corners where the old and the new wood were connected and which could not be reached with the router were sanded with a small round sanding device which was mounted on a Dremel tool.
The glass is test fitted and checked if there is enough space between the glass and the wood to make it able for the wood to expand and shrink without bringing the glass under tension.
When all is acceptable, the groove where the glass will be placed in is protected with two component epoxy.
The next step will be the fitting of the actual glass and creating a water tight construction for the sliding windows. This will be explained in the next update.
But first all will be sanded inside and outside since now it is rather easy to reach all wood of the steering cabin with all windows removed.
Maybe a useful tip the complete steering cabin including the windows can be removed for , for example transport or for removing one of the engines for major overhaul.
The unit including roof is bolted on top of the main cabin roof and sides.
In the front are bolts and nuts which are connected to a support fitted on top of the cabin roof.
Inside the cabin where the nuts can be seen through the support
The same situation is on the both of the sides of the unit where nuts and bolts are connected to internal supports.
The next picture shows the rubber seal between the two parts when removing the deck house one needs to perform this task carefully since it might be sticking together or even fitted with caulking.
Further all electrical cables need to be marked and removed before the deckhouse is lifted off the boat.
Bathroom Upgrade
The following part describes the work performed in the bathroom.
First step was to remove the toilet bowl which shows that a raised platform was made which I presume the reason was that the boat came deeper over the years in the water and if the toilet bowl is not raised it might overflow.
I found behind the toilet a hole in the wall to the kitchen cabinet which is a mystery for me and since I do not see the use for it will be closed.
The hole was made nice and square and a piece of marine plywood with veneer was inserted and glued in place.
The loose panels against the hull were removed actually all which could be removed was removed this include lamps and electrical wiring. All the walls were than cleaned and varnish removed till the original wood then all wood was sanded to get the original deep color came back.
Over the years due to the influence of the sun the inside of the boat has been discolored and looks yellow by removing the varnish and sanding the wood again the original deep dark color is returning.
The wall above the sink had so many holes that it would be impossible to close them all with plugs and still have a satisfying result.
To get a satisfying result thin, 4 mm, marine plywood with mahogany veneer was placed against the wall with contact cement.
The same situation was noticed under the hand wash sink where were a lot of old holes between the engine space and the bathroom.
Those holes were first closed with wooden plugs actually all holes were closed since I decided to make new holes for the water supply and the sink drain, this way be able to follow my own route of piping.
Also at this position a new 4 mm mahogany veneer wall was placed in front of the original wall with contact cement.
To make the new transversal walls matching with the side wall against the cabin also here were new plywood with mahogany veneer installed to make walls around the sink matching.
All the walls and all the wood of the bathroom were sanded to original wood and varnished with a two component varnish, several coats were used to get the deep rich color back of the original installed wood.
The grating of the floor was taken apart and all the pieces sanded and then rebuilt again.
The grating was protected with Owatrol D1.
Owatrol D2 is not used in this case since it will make the wood slippery.
The GRP shower pan under the grating was cleaned sanded and was coated with two layers of two component white epoxy paint.
A new panel was installed with switches and gauge for the level of the potable water tanks and the starting of the potable water pump.
Due to new rules and regulations it was decided to change from the original toilet to a so called chemical toilet. Since the space is relatively small first a template was made to find out if the unit would fit.
At one point when all is finished with the installed toilet and required accessories for the bathroom this page will be updated with pictures.
Rubbing stroke and Toe Rail
Before I removed the rubbing stroke and the Toe rails detailed pictures and measurement were taken this since I was aware that none of the removed wood could be saved nor re installed again.
Unfortunately with these repairs some pictures are missing due to a failure of my camera.
The wood for the rubbing stroke was cut from a larger plank and sanded and inside where it is mounted against the hull it was protected with two component epoxy.
The next step was to clean the hull where the plank would be mounted against and check if the area was a straight area so that a flush contact would exist between the plank and the hull.
Next pictures show before and after sanding.
The straight sides are not too difficult but for the bow which is round and slight curves up it are more difficult.
The same as with the beam under decks of the bow a template of carton was made.
Then from a plank with the same thickness the plank for the rubbing stroke was cut and was kept larger since I have seen in the past that when a perfect piece was made from a carton template that when the actual piece was installed on the boat that the wood was cut to small.
The plank was mounted with screws in the final position.
The next step was cut the top of the plank which was sticking out above the deck to make it flush with the deck biggest part was cut off with a multi-tool and then sanded.
Plank was removed again and cut with a small circular saw on the correct width.
Both bow rubbing stroke plank were fabricated the same way.
All planks were removed slightly sanded on the inside and glued with epoxy glue and screwed as well against the ship’s hull.
All was than sanded on the outside protected with epoxy and several layers of two component varnish,
Next step was to install a new toe rail on top of the deck.
Toe rails were cut with a circular saw to the right dimensions and the correct angle, measurement were taken from an old piece of toe rail.
I worked from aft to forward by installing the toe rail in the correct position on top of the deck.
Toe rails were screwed temporary into the correct position with stainless steel screws.
The length of the planks I used was 5 meter so the second part of the toe rail starts around mid-ships. With a strap and some tension was the toe rail put in position on top of the deck and screwed in place.
To be able to use this method the toe rail should be cut in the correct way from a plank with the grain of the wood following the toe rail otherwise it will be very difficult to bend the wood as well as that it will split.
It is impossible to bend the wood all the way around the bow and as used original the toe rail for the bow was made of laminated planks, original 5 thin planks were used but I decided that it was possible to do the new toe rail out of 3 planks.
The same method was used with a carton template to decide the curve of the wood on the deck before the actual planks were cut to seize.
The method I used was to bend and glue the new toe rail in place. First step was to glue the first two planks and then the next day the third plank.
Deck was protected with tape to prevent that epoxy glue would stick between the deck and the to be glued toe rail.
Then blocks were screwed onto the deck slightly in a curve which was larger than the curve of the deck where the toe rail would be mounted onto. The reason for this extra curve is that would glue together will try to come back into the original straight plank form.
As can be seen from the next pictures a lot of clamps have been used to glue both planks together and to hold the planks in the correct place.
The next day the third plank was glued to the first two planks as expected the glued plank would straighten a bit and were outside the original curve of the bow.
The third plank was glued against the first two planks but between the flanks and the wooden distance blocks on the deck an extra piece of wood was placed of different thickness to give the glued planks an extra curve so that when the glue was dry and the planks were removed and would bend back a bit they still would follow the curve of the bow.
When all was set and glue dried the bow toe rail was cut and sanded into the right form with angels and the correct height.
First step in this process was to sand the bottom of the toe rail flush and check if it was also with a flush contact with the deck before the rest of the toe rail would be shaped.
When all was prepared complete toe rail from stern to bow with the toe rail in place both side of the toe rail was tape placed onto the deck and the rubbing stroke.
This was done to prevent that epoxy glue would come onto the sanded deck and rubbing stroke.
The rubbing strokes were removed all was cleaned and the rubbing stroke was than glued with epoxy glue onto the deck as well as screwed in position.
An excess of colored epoxy glue was used to make sure that there was a 100% contact between the glue deck and rubbing stroke as can be seen for the next picture glue is coming out everywhere.
Since it is very difficult to remove the dried epoxy glue the next day and to shape it the glue was removed after the toe rail was screwed onto the deck, this was done with a tool as can be seen from the next picture to create a small curve between the toe rail and the deck and toe rail and rubbing stroke to prevent that water will enter between the two.
Next step is to remove the tape before the epoxy dries.
As can be seen from the next picture there is always a little epoxy creeping under the tape but since this is such a thin layer it can easily be removed by hand with some sand paper.
This is done at the same time that the toe rail will be final sanded.
Last step of the toe rail is the installation of the plugs which were glued in with colored epoxy glue as well.
Next to the entrance of the steering cabin is the position of the mounting plate for the railing.
When removing this plate I noticed that there was a gap between the wood and the top side of this plate.
Since I would like to have full contact between the two I made the position of this plate slightly higher to prevent in the first place that there would be a gap between the two but also to prevent that the support would rest onto the deck which prevents future maintenance to the wood.
The area under the stainless steel support is protected with epoxy and two component UV varnish
Last step was to sand all and protect the wood; this was done for the toe rail with Owatrol D1 and D2
What was left now is the toe rail/rubbing stroke of the stern.
This part is curved as well as that it is round.
I have tried to make this piece out of one piece but unfortunately my carpenter skills failed so I was left with the same procedure as used for the bow toe rail to build it up from different pieces of wood.
Actually I used 4 pieces these were cut from one piece.
The same as with the toe rail the boat was protected with tape to prevent that epoxy would get onto the teak deck and the stern.
Then the first piece was screwed against the stern in such a way that it would follow the shape of the stern.
First piece was with epoxy glued against this fixed plank.
When the glue was dry all was removed and sanded clean excess of epoxy.
Since this was the base for the rest of this plank it was glued with epoxy glue and screwed against the stern.
Same as with the rubbing stroke planks the stern was sanded flush where the new plank would be fitted against.
The plank as now glued with colored epoxy glue and screwed against the stern.
The next step was to screw and glue the next plank against the mounted plank onto the stern.
It was made sure since these screw holes with plugs are visible that the distance between them were the same.
Last plank to finish the complete structure was glued against the first 3.
All was sanded and protected with epoxy and last but not least protected against UV with two component varnish, 3 coats.
Finished installation of the two pieces of wood.
Fixed window installation
I’m still busy finding a method to make the sliding windows water tight but in the meantime all fixed windows have been removed and have been re-installed
I'm aware that an easy solution is to remove all windows and replace them with a new window frame and new windows but since I do want to keep the boat as original as possible and due to funds available I decided to install the old windows and find a solution for the sliding windows, therefore this part only explains the fixed windows and the sliding windows will be another chapter in this blog.
The first thing done to remove the windows, which were still as it looked to me fitted with their original white plastic stapled window cord.
Which that at one point I presume due to water leakage was tried to top with silicone.
As can be seen from the next pictures this did not stop the water ingress since the window is discolored with algae.
The pictures used for this blog have been taken from different fixed windows’.
The next steps was to clean the wood where the window fits in and remove all earlier applied varnish and protect the wood with two component epoxy two layers.
The first window I made the mistake, created a lot of extra work for myself by not properly placing tape on all areas where one does not want to have silicone.
For the first window installed I only taped the wood and nothing else, this was the mistake since it was impossible to get straight lines of silicone following the rims of the wood inside and outside.
After the first window installation I did follow the following steps.
Placing tape on the wood on the outside following the window frame taking time also to follow the round curves/corners of the wood.
Than the inside window frame was covered with tape although it is a small rim by not taping this piece of wood one has to clean the silicone of the wood while it is still wet, messy job or clean the silicone from the wood when it is dry with the chance of damaging the wood and the coating as well as scratching the window glass.
Than the window glass was placed into the window frame making sure that there was space between the glass and the wood for expansion/shrinking of the wood around the glass.
When the glass was in the correct position the glass was taped on the outside following the wooden rim on the inside this was when the silicone will be applied one will never look against silicone from the inside to outside.
Also take was placed on the inside of the window against the wood rim.
Then when all was taped and degreased with acetone wooden window frame and the actual glass the fun part starts actual installation.
A small layer of silicone is placed onto the wooden window frame where the glass will be fitted in, the amount must be such that when one pushed the glass into the silicone that between the glass and the wooden frame, inside, 100 % coverage is, in short everywhere between the glass and the wood silicone needs to come out.
When I was satisfied about the above, one or two windows I needed to remove due to not adding enough silicone, the silicone on the outside was installed.
To get a nice finish I used a plastic tool designed for this job.
When the silicone looks nice the area looks like the following picture.
Next is to remove the tape inside as well as outside to get a nice straight line of the silicone this needs to be done carefully by perverting to touch the silicone which needs to remain in place.
The tape is removed when the silicon is still wet to make sure that when the silicone dries it sticks to the window and the wood. When the tape is removed when the silicone is dry, this is possible without extra effort, I have noticed that there is a chance that where the silicone overlapped the tape that a minor gap is visible between the glass and the silicone.
I waited than 1 or 2 days and the excess of silicone on the window was removed with a razor blade being careful for not touching the actual silicone which holds the window in place.
I did had some challenges with the front and rear windows.
The main reason was the new wood installed at the bottom window frames although this was done carefully the window glass did not fit 100% in the wooden frame.
Although the next picture looks not professional by placing some wood and a strap over the window I was able to get a tight fit between the glass and the wooden window frame.
Letting the silicone dry for over 2 days a then removing the pressure from the glass resulted that the glass stayed in place and was well glued with the silicone against the window frame.
For the aft windows I used some nails by placing them against the glass I got a tight fit between the glass and the window frame.
Two days drying time and I removed the nails, the area without silicone was degreased again and a bit cut from the already installed silicone and fresh silicone was applied where the nails were installed.
The question is why I used black silicone instead of white which was original installed for holding the glass in place.
Main reason white window glass silicone is not UV protected resulting in discoloring to yellow as well as deteriorating over time.
Further I think the black silicone does not look too bad against the mahogany and it comes back in the deck caulking.
See also next picture.
Small autumn items 2013
Weather has not been so good and I have been occupied with my daily work so I have not been able to start with bigger projects.
Cable Tray in the Steering Cabin:
What disturbed me when I bought the boat were the loose wires hanging in front of the steering cabin windows for the window wipers.
As well as that the window wipers switches were mounted on big blocks against the top window frame, further cabling was for the search light, cables for the solar panels and a console light.
Looking for a solution to wrap these cables in a kind of a cable tray and to make sure that the cable tray in future would be accessible I came up with a construction of a mahogany cable tray against the top side of the window frame.
First job was to drill out all the old screw holes and plug them with mahogany plugs.
Plugs were glued in with colored two component epoxy trying to prevent any color difference between the plug and the window frame. As can be seen over the years a lot of screws entered the window frame.
Next step was to sand the plugs flush with the window frame and varnish in two coats the window frame.
The actual cable tray is made of two pieces a square 10 X 10 mahogany piece which is crewed against the window frame, due to the small seize and cutting the wood with the right grain it was possible to follow the curve of the top of the window frame.
About 12 mm was kept as a width for placing the cables in, so the actually cable tray will be 12 X 10 which is just enough to place the required cables in my case.
For the window wipers I do use a multicore cable easier to insert in the cable tray.
The cable tray comes down on port side and will run into the direction of the steering console.
The cable tray is closed with a flat piece of wood which cover the square support and touches against the white ceiling.
This is a flat piece of mahogany of only around 4 mm thick; due to the limited thickness I was able to bend this also in the curve of the window frame.
It is a bit under pressure but not that much that the screws do not hold.
Next picture shows the starboard side of the finished cable tray, at a later point the complete cable tray will be closed when all wires are pulled.
The strip in the middle of the ceiling which covers the sides of the soft ceiling tops was loose and did not completely cover both sides anymore.
Since this did not look very nice and since I needed a cable for the search light I made mahogany strip from forward to aft in the center of the ceiling which can hold two flat wires.
Next picture show the loose hanging strip in the middle,
I took a flat as possible piece of mahogany trip sanded the sides round made with a router two grooves on the inside, one for the cable for the search light which comes out fairly at the beginning and one for a future purpose for example a light in the steering cabin.
The cables were glued into the grooves.
Next picture shows the removed original strip as can be seen there is space available for placing a wire between the two soft ceiling panels, one has of course to be careful with screws of nails for not penetrating the cables.
In my case the two grooves for the cables were left and right of the center line of the wooden strip and therefore there was no chance of penetrating the cables.
Before the trip was installed it was twice varnished inside and outside to protect the wood against the weather it was than installed with brass screws against the ceiling.
At the front of the plank the two wires are coming out and will be guided in a later stage properly into the cable tray.
Next picture shows the finished strip screwed against the ceiling.
Main Cabin Ceiling Light
Originally the cabin ceiling light was round and as I can imagine the light might not have been very effective to read or to have a nice dinner, not enough light above the table.
Over the years before I bought the boat the round light has been replaced by a block of wood with 3 halogen lights, this block is rather large and in my opinion does not fit into the interior of the boat.
The above mentioned construction was removed and a new construction of mahogany was made which is thinner and smaller also in this piece of varnished mahogany 3 halogen lights were positioned above the table.
I think the new construction fits more into the interior of a classic wooden boat.
Storage Bin steering cabin
A while, few years, ago I noticed that a part of the aft port-side floor board was rotten away as well as the support beam for the floor board mounted against the storage bin.
The first part I did was to remove the rotten beam and replace it with a new beam.
I left it for awhile but further investigation at the end of last year showed that the front wall of the storage bin was rotten as well and did not give enough support for the floor beam as well as that the front panel was badly damaged. It was then decided to replace the rotten wood of the storage bin completely good thing is it is only the port side bin .
Since I did not know how the storage bin was built together I started slowly taken it apart and actually it is not a simple construction as I expected.
I did not take any pictures during the dismantling of the bin but will describe how I built it together again.
When the complete bin was taken apart I ended up with a lot of small support wood for the actual bin.
All were sanded and varnished, due to the outside temperature I took them home and placed them in a warm area for curing between the different layers of varnishing.
A small electrical heater does wonders.
Several of the small pieces of wood are from the inside windows between the main and forward cabin.
With the whole storage bin apart I had now also the opportunity to make a proper heat resistant blanket around the exhaust of the cabin heater.
New inside panel was made this is an important panel it holds several support wood squares for the floor in the bin as well as for the top cover and front wall cover.
I have copied this panel as well as drilled the holes for the screws in the same place.
Pictures or a drawing is important when taking this panel apart since on both sides square support wood is mounted. Although difficult to see one can notice the two rows of screws.
The bin bottom support against the aft wall is screwed against the new the new side wall panel from behind with screws one does not notice when the unit is taken apart.
The next picture shows the support planks against the inside aft wall panel.
There were a few nice warm days and I was able to sand and varnish the inside aft wall of the bin.
The wall was varnished also at the area where the floor support is mounted against the aft wall.
The new bin is than put together with the side wall and the front wall both made of marine plywood of which the front wall is with a layer of mahogany veneer.
All has been protected with varnish or the front panel with a layer of epoxy and two layers of epoxy varnish to give it more strength against future damages.
Next part to be installed is the support for the top cover with drain inside.
Also this wood has been protected around with varnish.
Although difficult to see the transversal support for the longitudinal side wall of the steering cabin is connected to the front wall of the storage bin.
Although the picture does not show this this support was still in a good condition.
Took me some time to find out why I could not remove the front wall when all was loose according to my opinion.
To reach these screws the complete side wall needs to be removed. Which also result that several support beams of the floor need to be removed as well.
The hatch and top cover were cleaned and as one can see I did not have too much trouble with removing the old layers of varnish.
After properly sanding the more or less yellow color was replaced by the original deep wood color of the mahogany. The hatch and the rest of the cover were protected with two component epoxy varnish, 3 layers to protect it against future damage. This also resulted in that the deep shining mahogany color came back.
Last thing which was done after all was screwed together was to glue plugs in and sand the complete top cover slightly.
A final coat of epoxy varnish will be applied when all work has been finished in the steering cabin.
As can be seen from the next picture there is a little gap between the top cover and the walls, this gap will be filled with Sikaflex to prevent that water can run into the storage bin.
Small Hull Damage
The plan is to paint the hull above and below the water line this summer.
Above the water line with a finished coat and below the water line just the protective coat , anti fouling will be added before the boat will be returned to the water.
The painting process will be a different chapter in this blog.
Before is started to sand the hull I checked it once more for other hull damages.
Although I was aware of them I decided this time to repair them in a way which is in my opinion better than as original planned.
The original plan was to fill the small 5-10 mm deep holes with putty or any other kind of wood filler.
I'm afraid that over time water will get behind the filler resulting that the wood will rot away with the chance of more damage to the hull than the present small holes.
It was decided to drill the bad wood out and replace it with a wooden plug which would be glued into the hull.
First in the center of the wasted wood a small hole was drilled as guidance.
The second step was to drill the hole on the size of the plug .
The plug was fitted and glued in.
The biggest challenge was where do I get a mahogany plug of +/- 21 mm and a wood drill of 21 mm.
The size of the plug was decided by the hole saw I had, as we all know the trick of the hole saw is the drill in the middle which would have me ended up with a plug with a nice round hole in the middle, something one would like to prevent.
What I did was that I placed the holes saw in a stationary drill.
The next step was that the drill bit was kept as high as possible into the hole saw to prevent that the plug would get a deep hole in the middle.
The wood for the plug was chosen thicker than the actual thickness of the hull resulting that the plug on the inside cut be cut to length after the glue had cured.
As we all know the hole saw diameter is decided by the outside dimension and not the inside dimension.
To get a plug which fitted I first drilled with the hole saw the plugs, than measured the plugs and started to look for a wood drill of the same dimensions which I did not had nor could buy.
To make sure that the plug would fit tight in the hole I grinded a wood drill, as in the picture to a smaller dimension. Both side were grinded till the desired dimension was reached.
This resulted that the home made wooden large plug would fit tight in the drilled hole.
Keel Repairs II
August 2014 Keel Repairs Continued
After replacing the keel of the bow in 2013 most of the work has been concentrated afterwards on other projects.
This summer a start was made with the painting of the complete under water ship and the hull.
After the underwater ship has been scraped from the antifouling paint and base coats a further inspection was made of the keel.
The stainless steel rubbing stroke was removed from the keel between two supports, it was noticed when the stainless steel strip was removed that sikaflex was standing like little mountains on top of the strip indicating that there were cracks in the wood.
The wood was cleaned and indeed there were some cracks in the wood and the sikaflex covering the bolts was loose. But the things did not look too badly.
A layer of Priomacon paint was applied as protection. Upon further inspection after the paint dried the wood did not looked to good.
Since it looked like that the cracks were not too deep it was decided, to use a router and remove the wood which was in a bad state.
There is approximately 20 mm wood removed till wood was found in the keel with only hairline cracks.
Wood was cut to seize and dry fitted it was slightly thicker and the depth of the groove, to be able in a later stage sand all smooth again with the original height of the keel.
The next step was to glue with epoxy a new piece of wood in the large groove made in the keel. The good thing was that the cracks were only ion the middle part of the keel and not running into the sides. The new wooden strips were hold in place with screws alto to make sure when screwed ion place that excess of epoxy was compressed in the little cracks left in the keel.
When all was dried the new wood was sanded to the correct height of the original keel.
Screws were removed.
The screw holes were drilled out and filled with wooden plug which were glued in place.
All was sanded again and painted several coats with Primacon
In a later stage the stainless steel strip will be glued back again with sikaflex and stainless steel screws.
Overboard Connections
August 2014 Overboard Stubs removal
To be able to perform a good coating of the under waterline hull and the above water line hull it was decided to remove all overboard stubs.
Another reason was that I did not know nor could find out when was the last time these were removed or replaced.
This is where the challenge started not only are some of them difficult to reach but like with new over boards there were no notches on the inside of the stub, to hold them in place when one tries to loosen the nuts on the inside of the hull.
Next picture shows a new overboard stub.
Several tries with different tools, cleaning of the thread and some heat it was still impossible to turn the nuts loose or completely off the overboard stubs.
One of the main reasons was that the overboard stubs did not have the notches in them to keep them in place from the outside. They kept turning and could not be fixed in place to loosen the nuts.
The only thing left was to cut off the flange of the overboard stubs and push the actual stub inside the boat.
As one can imagine this has to be done very carefully to prevent that too much damage is created onto the actual hull.
Pic 3
The best method I found was to cut off the flange with a Dremel tool with a cutting disc.
Started with a normal cutting disc in the largest overboard stub, toilet outlet, and when the cutting disc was smaller wear and tear, moved to a smaller diameter overboard stub.
With this method all flanges of all over boards were removed.
When the overboard stubs were removed I had the feeling that some of them have never been removed since the boat was build. The impression was due to the materials used that they have been in the hull since day one.
After the removal they were inspected and were actually still in good condition.
The holes were cleaned out and I noticed that they were not protected by paint which I will do.
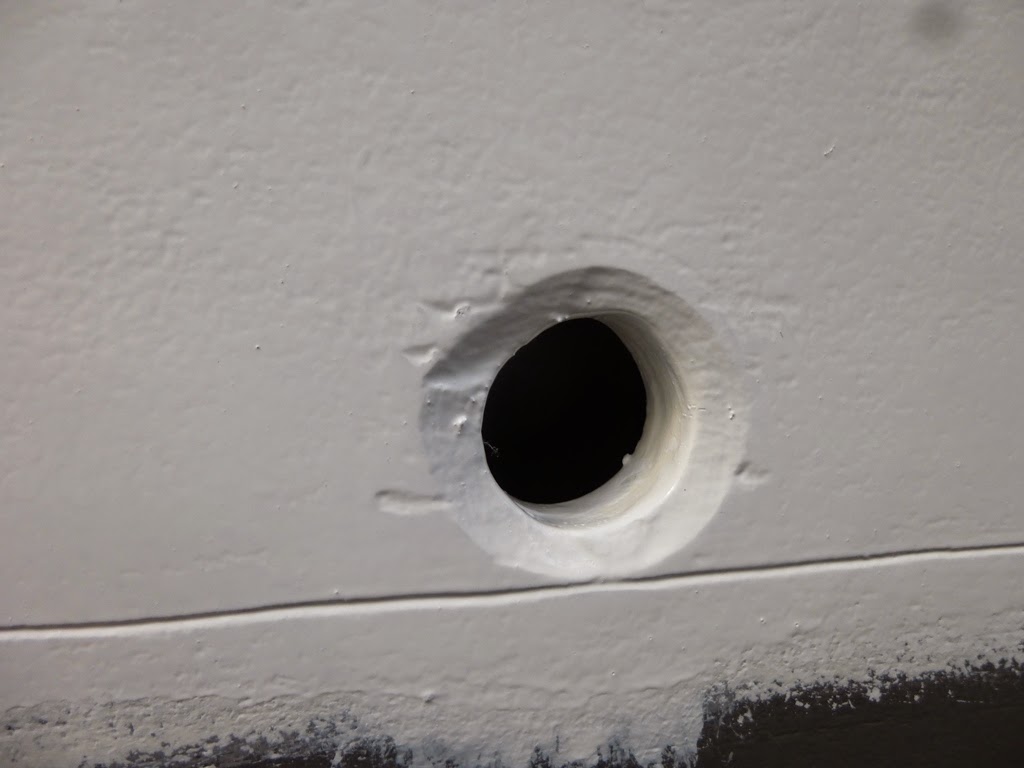
New overboard stubs will be installed after the painting has been finished and since I might sail with the boat in salt water the underwater overboard stubs to be installed which are made from Bronze and the above the water line from Brass.
Keel repairs III
Keel repairs III
This will be the last update on the keel repairs since some items were not covered in the earlier blogs with regards to the same subject.
When the stainless strips are removed, most of them fell off by themselves, one can see that when they were mounted the last time that there has been not a full surface contact between the stainless steel strip, sikaflex and the ships keel.
This could also be the reason that the wood started to deteriorate at the point where the sikaflex touched the wood, open voids between the two.
Other reason could be that bronze or brass screws which have been used to fix the Stainless steel strips against the keel failed. In my opinion this created a “Battery” with the result that the screws fall apart over time and therefore lost their strength to fix the stainless steel strip against the keel.
With the removed strips wood was repaired where necessary as explained in earlier blogs.
We are now at the point that new wood has been inserted painted several times with primer for the underwater paint, 6 coats, and we could start with installing the stainless strips again.
The strips had a lot of old paint and this was removed as well as sanded to make sure that a good contact would be created between the stainless strip and sikaflex. The sides were thoroughly cleaned as well.
During the cleaning of the strips it was noticed that there was some wasting of the stainless steel at the points where the keel bolts are positioned in the keel, which gives me the indication that the stainless steel is not 316 but 304.
When all was cleaned to my satisfaction the stainless strips were cleaned with acetone for degreasing them, same was done with the keel.
The stainless strip was 100 percent covered with sikaflex Seal and Glue and screwed with stainless steel screws against the wooden keel.
A large amount of sikaflex was pushed out between the two and this was removed.
Last step after removing the excess of sikaflex was to turn all screws a quarter of a turn, could not turn them anymore, to get a little more sikaflex out and create a small roll of sikaflex on the side of the stainless strip.
At this moment it could also be checked if there was 100 percent surface contact between the strip, sikaflex and keel.
Last repair item on the keel was a small damage on the starboard aft bottom side of the keel.
I could have filled it with wood filler but since I would like to make permanent
repairs and did not know how much wood was rotten and the wood of the affected area was removed.
New wood was glued in and fixed with stainless steel screws, bearing in mind the grain of the insert.
At the same time some holes above the removed wood were drilled out and filled with plugs.
All was sanded smooth and painted with several coats of underwater paint.
Engine Air inlet
During the dismantling of the teak deck it became clear that water was going into the boat through the slotted hole in the deck near the steering cabin. This resulted that in my case the inside deck beam, under the deck house, was rotten away.
Of course there always will be the chance that water will enter this area due to the opening at the front of the cover, with rain or bad weather during sailing.
When removing the fiber glass panel’s port and starboard it was noticed that these were glued against support wood and on top of the teak deck.
At the same time it could be seen that a seal of silicone on top of the deck should prevent water from entering the opening in the deck.
For me this is not the right solution but must have been a good solution when the boat was designed, not the same types of glue/epoxy available.
The disadvantage of gluing something onto a teak deck is that teak is a greasy type of wood and it is difficult overtime to keep a good seal.
The Fiberglass covers were positioned onto the deck hold in place and with a pencil the outside was drawn onto the deck.
From there measurements were made to decide the width of the slot into the deck.
Then pilot holes were drilled into the deck at the center-line of the too be created slot.
With a whole saw larger holes were made to be able to remove the wood for the slot into the deck.
Made a minor mistake in measuring and ended up by removing wood of the deck in way of the wet unit. This was closed with epoxy at a later stage.
The wood of the deck was removed between the two outer holes by means of the help of a multi tool.
Next step was to create a barrier between the deck and the opening by means of a fiberglass “box”. With duct tape a barrier was created between the deck and the slotted opening.
When all was taped close a wall was created with fiberglass cloth and fiberglass against the duct tape but also against the cabin structure as well as against the whole slotted hole, wood was completely covered with cloth and epoxy.
After the tape was removed a small thin ‘box” of epoxy was created into the deck.
Several more layers of cloth and epoxy were added to create strength of the “box”. Also to make sure that there were no holes between the box and the deck an extra layer of epoxy was added at the outside of the “box’ to make sure that there is a watertight seal between the two: box and deck opening.
When all was finished to my satisfactory the box was tested with water on deck and no water passed through, the lowest part of the ”box” is higher than the toe rail so the chance that water will enter the engine space with water on deck will be minimum.
The following step was to recondition the fiberglass covers, wood from the inside was rotten away as can be seen on one of the first pictures and the type of paint used was normal white paint.
After al was cleaned and sanded I noticed 4 mall holes and a bigger hole on the covers.
Placing the navigation lights on the cover the holes matched up with the mounting holes of the navigation light.
Inside was cleaned and loose materials removed and new support wood was made to fit.
This wood was glued with epoxy against the cover approximately 2 mm lower than the cover rim. This way creating space for a seal.
When all was fixed the complete inside was painted with two component paint as protection for not only the wood but the fiberglass as well.
Since I do not plan to permanent fix the covers against the deck house I have been looking into an installation which allows me to remove in not a too difficult way these covers.
Main reason for removing the covers is that once a year I need to protect the wood with Owatrol D2, if the covers remain in place it will be difficult to protect the wood behind the covers.
Covers are fixed with screws original from the inside.
The solution I have is to place the same type of rubber as between the deck house of the steering cabin and the cabin walls.
This rubber was glued with sikaflex, after degreasing of course, onto the wood in the inside of the covers.
This was done with staples and later a thin layer of sikaflex was placed over the rubber with staples. When one does not degrease than the sikaflex will fall off after drying, after degreasing it sticks to the rubber.
Before the rubber seal was added the cover was sanded and painted twice with sanding in between with two component epoxy paint.
The covers were mounted onto the deck house and with this type of seal I can remove them whenever I do require.
As can be seen from the below picture no seal was added between the bottom of the cover and the teak deck, this way no water will be collected between the two and I do expect with the above described construction that the deck and the slotted opening will remain intact over the coming years.
What is left now is the decision where to place the navigation lights on the covers which I do prefer since if there is a water build up between the navigation light and the cover it will not affect either of the materials. When placed where I did remove them at the corner of the steering cabin on the wood there is again a chance that the wood will be affected and will start to deteriorate.
Below some pictures of the navigation light mounted onto the engine inlet cover.
If any of my followers do have the same set up on their boat I would like to hear from them and if possible with a picture.
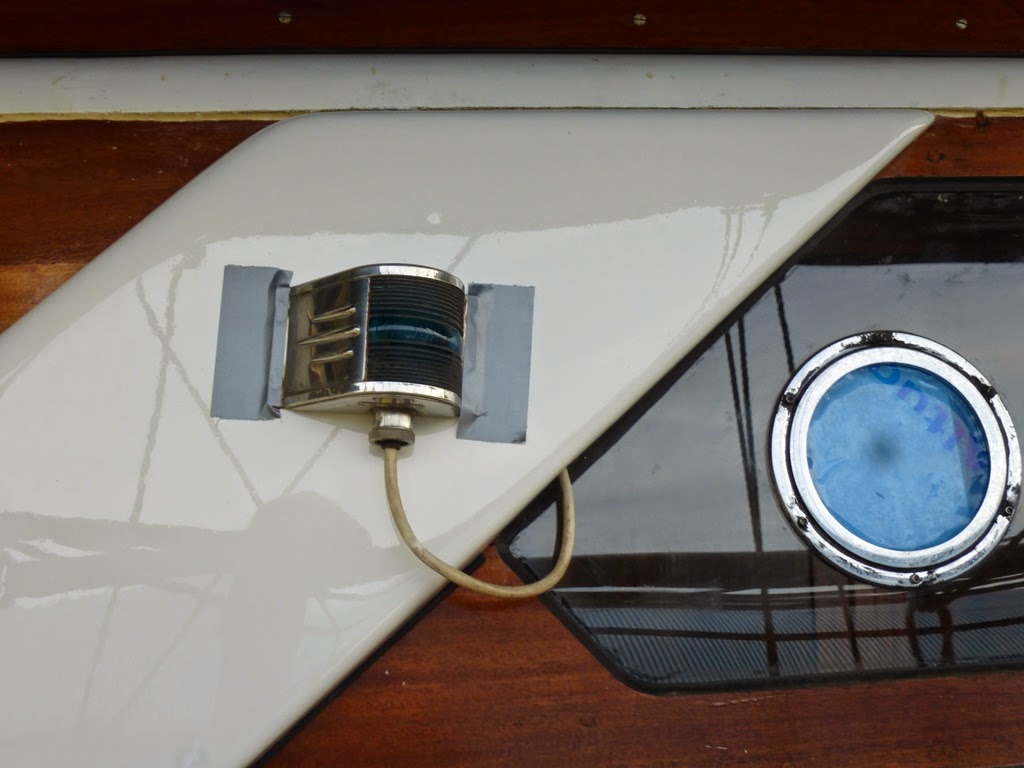

Hull Painting above and below the water line.
Although it looks like most of the below described work was done this year it actually has been taken place over several years due to the extensive repairs onto the hull and other maintenance which I thought was required before even starting on the painting of the hull.
Also since the hull is made from wood the paint choice might look easy but it took some time to decide, lost of information from the internet and specialist I know through my daily work before a final decision was made for in my opinion the best paint for the boat.
I have chosen to go with International paint system.
Above the water line with Yacht primer, Pre Cote and Toplac, below the water line Primocon as primer and a later to decide anti fouling paint.
As can be seen from the next picture the paint was in such a condition that I took the decision to completely strip all the paint of the boat and start all over with a new paint system.
First step was to remove all algae and shells which had grown over the years onto the hull.
During the course of the hull repairs paint was removed where required and where old and new wood were joining the hull was sanded smooth.
After sanding the wood was protected with several coats of virgin linseed oil.
At a certain stage of above mentioned repairs the complete hull above the water line was removed from paint, scraping and sanded smooth followed by treating with linseed oil.
This year the plan was to paint the above and under water line, more or less the complete hull.
First step was to remove the linseed oil from the hull and sand the hull again smooth before the primer would be applied. This was not as easy I was hoping for since the linseed oil although it entered the wood also build up a layer on the outside of the wood, could not be easily removed.
Sanding was not possible since the paper was full within seconds. Only thing left was to scrape the hull clean again from the applied linseed oil.
After all linseed oil was removed the hull was sanded smooth.
Hull was then cleaned from dust and degreased with acetone followed by the first layer of yacht primer. The first layer was diluted with thinner to make sure that it would impregnate the wood.
After the first coat of primer one could also good see the deficiencies in the hull which are not so clear after sanding.
Those were filled with International Watertite filler, the spaces between the planks were not filled those will close naturally when the boat gets into the water.
All was sanded again to my satisfaction.
Than another 3 coats of yacht primes was applied as per manufacturer’s recommendations.
The following step was to apply 2 coats of Pre cote an intermediate paint between the primer and the final coat.
Before the final paint was applied the surface was lightly sanded with grid 320 to create a smooth surface. The final paint I used is TopLac white, 3 layers were applied.
Before
After
Before the boat will be launched another two layers of Top Coat will be applied, of course after first sanding and degreasing the present installed finished coat of paint.
The below the water line anti fouling was in reasonable condition but I did not know which paint system has been used therefore all paint needed to be removed.
First stage was to remove the growth on the hull.
Then from the complete hull the anti-fouling paint was removed with scarper and hot air gun which mainly has been done by my wife.
As can be seen, red paint, which I presume is the old fashioned wood protecting primer, most likely with led, I left on the wood since it was in a good condition.
After scraping came sanding, since it is under the water line the surface was sanded but not till a very fine grid, last paper used was with grid 180. For better access to the hull the propellers with shafts were removed as well the rudders. Both systems require attention as well which will be worked on in 2015.
First coat of Primacon was applied which was diluted with thinner as per manufacturers recommendations. Than the small holes, mainly where the plugs for the rivets were inserted were filled with two component filler. I have used the International filler to make sure that there would be a good bonding between their materials, filler and paint, this way preventing the chance that there would be over time separation between the two.
Before the boat will receive its antifouling paint the hull, below the water line will be lightly sanded again and two more coats of Primacon will be added before the actual anti fouling is applied.
After all was sanded smooth 3 more coats of Primacon were added. Following pictures show the present condition of the boat.
One of the reasons I choose to use International paint is that the primer for the antifouling can remain for a long time unprotected and it is not required to apply the actual anti fouling paint within certain months or weeks onto the primer. This is required for most of the competitions antifouling paints, primer cannot be unlimited exposed to air.
.
Teak Deck Installation Part II
Due to my day to day work, need the money to finish the boat, I have not been able to spent too much time the last 12 months on continuing with the repairs, the same is expected for the next year. I have been working on the boat but most of the repairs were repeat repairs of earlier described work onto the boat.
Although it looks like a long time that I took to have the caulking cure of the teak deck this was intentional. Idea was to finish the outside roof of the main cabin first before continuing with the deck. Will describe the roof of the main cabin painting in another blog.
We continued where we left the teak deck after calking between the planks.
The first thing to do was to course sand the teak deck, grade 40, to get all the excess of caulking of the deck, when this was done the deck looked great, from a distance.
A closer look showed that there were area’s in the calking which showed smaller and some larger holes. One can leave these smaller holes in place but as I have seen, even under a tiny hole in the caulking a large hole can be present. Reason for these holes can be to quickly filling the groove between the planks with caulking, not taking enough time to fill the groove completely, working slowly and diligent. Or when one starts with a new tube of caulking and forgets to let the air out.
How to solve the issue of the holes, one need good tools: sharp knife and I used a chisel slightly smaller than the groove. One then carefully cuts the caulking out of the groove where the holes are. I cut all the caulking out till I reached the wood to make sure that no holes in the caulking would be present. Also cleaned the sides from caulking.
Next step is to place masking tape on the sides of the groove we do not want to get to much caulking onto the sanded teak deck again.
Clean the groove make sure all the dirt and loose rubber and wood are vacuumed out completely, prepare the groove with Sikaflex primer, Sikaflex is the system I used but as mentioned in my earlier blog there are other suitable caulking’s for teak decks. Most important is to follow the manufacturers instructions and do not make short cuts.
The following step is to fill the groove with caulking and use a putty knife to make sure that the groove is full and that the caulking is not sticking to high above the deck.
Reason for not having too much caulking sticking out above the deck is that sanding will be more difficult as well as that when there is too much caulking onto the tape that the tape cannot be removed before the sanding is started.
With a little thin layer of caulking onto the tape, the tape can be removed after the caulking has dried. If the tape cannot be removed one needs to sand it off, which will make the teak deck dirty with glue from the tape
What is left then is sanding of the area’s where new caulking has been filled into the groves between the planks. As can be seen from below picture there is no difference between older caulking and new caulking .
Rudder Bushing
During the scraping of the bottom I did found some silicone around the nut of the starboard rudder bushing. I did not pay much attention to it until later this year when we started to paint the inside of the boat under the water line.
What I noticed was that the bushing from the inside looked a bit loose and further investigation from the outside showed that there was quite an amount of silicone placed around the nut, more or less covering the nut, could be to protect the vessel from water ingress.
Could not find any information on the internet about this rudder bushing how it was installed or fitted into the hull.
So I started to dismount the area. First thing to do is to remove the arms from the actual rudder stock.
Next step is to remove any damage scratches from the rudder stock to prevent when the rudder is pulled through the rudder bushing that scratches can occur on the bronze bushing which can create friction when the rudder is placed back.
Also the compression nut for the packing is loosened.
The rudder is then removed.
To be able to remove the bushing with gasket one needs to remove the plank above the rudder bushing.
When the support plank is removed the compression nut for the gasket after which the two lock nuts can be removed to be able to push the rudder bushing outboard.
In my case when I start to remove the compression nut for the gasket the complete rudder bushing started to turn resulting that I was able to pull the bushing inside.
Next step was to clean all thread bushing inside the compression nut removing the gasket. Checking the hull of the ship for wood rot and to my amazement the hull was sound no rot could be detected, hull inside was cleaned as well.
Inside the compression nut is the gasket which was removed to be changed for a new one, this is pretty easy when all is removed compared to when the complete construction is in the boat.
As can be seen from the next picture the gasket material was not properly inserted, one should not make one long gasket like a spiral but one should make individual gaskets for each turn this to make it able to compress the gasket better.
When all was cleaned and de-greased with acetone the bushing was placed back into the hull.
To prevent that when the locking nuts were tightened inside that the complete bushing would turn again, like when the bushing was removed the outer nut was installed with thread lock.
Next step was to install the bushing in place and to seal it against the hull, for this I used seal and glue, as from the picture can be seen I used an excessive amount to make sure that I would have a guaranteed 100 % sealing between the rudder bushing and the ships hull. Excessive amount of sealant glue was removed shortly after the installation.
Nuts were tightened on the inside, rudder installed and new packing placed.
The easiest way to cut packing on the right length is to pull the packing around the rudder stock make a small cut as reference point then remove the packing and cut under a 45° angle on both side the packing to the correct length. Insert after the rudder is in place with the 45° cuts on top of each other. This way when the compression nut is tightened each individual packing will be compressed. When the packing is installed the wooden support can be installed as well.
Below pictures are from the propeller shaft packing but the principle is the same.
Kitchen painting
As with all other areas which required painting or repairs it was also decided for the kitchen area to take it apart and remove as much as possible the wood which can be removed for proper sanding and painting as well as inspecting the condition of the wood.
After the paraffin cooker was removed the base of for the cooker was removed, one can see that this is not an original design for the position of the cooker, it looks to me that the original cooker has been removed and replaced by a Taylor cooker.
When the 6 screw in the wood were removed it was still impossible to remove the plank
After
The reason that the plank could not be removed was that there was another screw holding the plank in place which was located in the storage cabinet under the sink area.
With the removed plank it was now possible to get behind the cold storage area and clean it out , as can be seen lots of different things ended up over the years behind this cold storage from a ceramic serving dish to snickers and tea,
With stainless steel plates removed one can clearly see that in the past a cover must have been in place to close the cooking area, most likely the Taylor cooker is higher than the original delivered cooker. Light line on below drawing shows that a wooden support strip has been in place in the past.
The bottom plate where the cooker is positioned on has been sanded to bear wood and has been protected with epoxy varnish 3 layers to give it a stronger protection than with normal varnish would be accomplished.
Bottom plate has been installed again as well as the stainless steel side plates to protect the wood from heat during cooking.
The next area to be sanded and varnished is the cabinet next to the sink and cooking area, in my case this area is set up with and area for safe storage of plates cups etc.
The shelf's were taken out and apart and all separate sanded and varnished, when one does this it is important that pictures are taken because with all parts of the two shelf's as loose items it is a challenge to get them correctly back together.
The bottom shelf was not mahogany nor it had mahogany venire it was just a plank of plywood.
To make it look a bit better it was varnished with a varnish with a so called Mahogany varnish which as we all know comes out to red , so I mixed some oak varnish with the mahogany varnish to give it a bit more realistic color. This bottom plank is screwed in the bottom onto the ships structure all the way forward, difficult to reach and in the middle and aft side.
The hull behind the shelf was sanded cleaned and treated with linseed oil .
The planks near the window frame were also removed and sanded and varnished next picture shows the bottom shelf and all other planks installed of the cabinet .
Next step was to install the shelf's for the cups and plates, this units although looks like one when in place can only be removed and installed in two pieces which need to be disconnected from each other for removing. First section installed which di not work out correctly and needed to be removed again
First section to be installed is the below section in the picture
Second section to be installed is the below section which holds the cups.
The whole unit is fixed to the ships structure with different strategic installed screws which normally are closed with wooden plugs, those were installed after the pictures were taken.
The whole unit in place and ready to store the plates and cups etc.
Sliding doors were in a good condition only required a good cleaning.
The Steel shelf was coated again with a new layer of plastic with self adhesive.
The next two pictures showing the finished product.
As can be seen from the below picture the complete kitchen block was sanded all planks doors which could be removed were removed to be able to proper sand and varnish the wood, hinges were removed and cleaned from earlier applied varnish.
Kitchen block completed
Taylor cooker was overhauled and works as it should be again.
One of the reasons that I keep cooking on a paraffin cooker is that I think Taylor makes a good cooker as well as I think that it is safer on a boat to cook with paraffin tan with gas especially a boat as the Storebro where it will be difficult to create an area for safe storage of gas with an outlet overboard.
The wall next to the sink was clean sanded and varnished again the differences in color of the wood are gone now as well as the discoloring due to earlier leakages.
As can be seen from below pictures although everything looks good I was missing a cover for the cooker.
From some scrap Mahogany planks I made a cover to protect the cooker and create some more working space in the kitchen area as can be seen from the below picture the kitchen is finished now.
Propeller shaft Bearing
As expected the Propeller shaft bearing outside was deteriorated and needed replacement .
Since the bearing is tight in the bearing housing which is bolted against the hull it is not sensible to try to hammer the bearing out of the housing, In the first place when on add force to the bronze part of the bearing by hitting the metal it will expand and the actual bearing will get tighter in the housing. The other way is to remove the complete housing from the boat and then press the bearing with a hydraulic jack out of the housing, but then there is a chance that the bearing housing will not end up in line with the engine which will create another additional job.
To prevent both above options I decided to cut a groove in the bearing until the bearing housing. This was done with a Dremel tool and a small router suitable for metal, this is a slow process and one should make time to make the cut. I first tried it with a saw blade but this is not easy plus the fact is that it is very difficult to keep the saw blade straight in line with the bearing..
The following two pictures show the end result of the cut in the actual bearing.
When the cut is made it is easy to knock the bearing out of the housing with a hammer and a piece of wood, this since the tension is gone from the bearing which holds it in place in the housing.
The bearing housing is cleaned and checked for damages. Then the new bearing needs to be inserted and as mentioned in the beginning it is not a good idea to try to hammer with force the new bearing into the housing, For example if it is not lined up properly it will result that the new bearing will get stuck in the housing which will result most likely in removing it and having to buy a new one.
In my opinion the best method is to slowly pull the new bearing into the bearing housing. This was done with a threaded rod and some plates covering the bearing at one side and the bearing housing at the other.
The bearing was lubricated with some oil and by turning the nut on the threaded rod the bearing slided relatively easy into the bearing housing without getting stuck. It is important with this method that the threaded rod is exactly in the middle to get an even force onto the bearing when it is pulled into the housing. As well as that the rubber of the bearing will not get damaged by the threaded rod.
As can be seen from the next picture the bearing housing is fitted with a new bearing which will last for several years. This was done for both propeller shafts.
The removal and installation of the actual propeller shafts will be another chapter of this blog.
Propeller shafts are planned to be installed this summer 2016 .
Escape Hatch forward bedroom
August 2016
The original escape hatch was mounted on plywood which was screwed on top of the deck.
Since I had some thick mahogany left I decided to make the wooden support for the actual escape hatch from mahogany instead of marine plywood.
One of the reason was that I did not have to paint the marine plywood in a wood color on the outside as well as that the mahogany is in my opinion better resistant against the weather than marine plywood.
The first step was to get the exact dimensions of the too be made wooden ring from the actual escape hatch.
I used an old trick to get a perfect circle, small plank nailed to the center of the ring and a nail on the outside of the small plank for scratching the circle into the wood.
This was done twice, than the scratch was followed with a pencil to get a good visible line.
The next step was time consuming with an electric jig saw to cut circles and ending up with a round wooden circle, support for the escape hatch.
The actual escape hatch ring was placed on the wood to check for roundness and to predrill the holes for mounting.
What I noticed is that the holes are not all on the same position from each other resulting that the escape hatch ring can only be placed in one position onto the wooden ring.
After the hatch ring holes were drilled the holes for mounting the wooden ring onto the deck were drilled and it was made sure that these screws would not stick above the wood.
The whole wooden ring was than sanded and protected with two component epoxy varnish.
It was made sure that the holes were filled with epoxy varnish as well to protect them from water ingress.
The ring was then left alone for almost a year to make sure that the wood would not crack or would show hair line cracks.
The next step was to mount the wooden ring onto the deck; this is a slow process since a measuring the center of the escape hatch takes time.
If it is not measured correctly the hatch will not be in the middle of the underdecks support wood and in the middle of the deck beam which needs to be cut.
Although from outside it will not be visible that the hatch is not exactly in the middle from inside it will be very clear.
When the middle of the escape hatch was decided a pilot holes was drilled and in the inside the position was confirmed.
Then with a jig saw the round holes was cut out of the deck, very slowly to make sure that in the end we do have a round hole.
It was then checked if the hole was under the right angle but when one holds the jig saw straight onto the deck than this should be no issue, all was straight in my case.
This cut out hole for the hatch gives at the same time the opportunity to check if the installation of the teak deck was done correctly and as it shows on below picture all was as expected.
The ring was fitted again on deck this time positioned and screwed temporarily onto the deck.
The cut holes in the deck was checked and sanded to get a smooth surface and some high points in the cut as a result if sawing the hole were sanded as well.
It was then looked in how to cover the inside of the round circle of the deck opening, original this one was painted white.
My idea was to place veneer onto the complete inside opening covering the new wooden ring on top of the deck and the actual opening in the deck.
After several attempts which did not look good it was decided to paint the opening in the deck white and this was done with several layers two component epoxy paint.
The wooden support ring onto the deck was kept the same.
The next step was time consuming which was placing protective tape onto the deck inside deck and around the wooden ring to protect them from caulking when the ring was mounted onto the deck.
For this purpose the ring was screwed again onto the deck.
To make sure that there will be no water ingress between the wooden support ring mounted onto the deck and the deck a small rim of the wooden ring was left unprotected to be able the have the ring where it meets the deck been glued with caulking.
The wooden ring and deck where then degreased and the ring was screed with caulking onto the deck.
After all was set and inspected that for 100% the caulking was coming out between the wooden ring and the deck inside and outside the extra caulking was removed as well as all protective tape.
The caulking was left a week to dry and the escape hatch was temporarily closed with some Plexiglas.
In the meantime the actual escape hatch was mounted together from all loose parts which were re-chromed.
A new Plexiglas window was fitted.
To protect the inside form excessive sunlight as well as from preventing that people will look inside a mirror foil was added to the Plexiglas before it was fitted in the escape hatch frame.
One can look from inside to outside but not from outside to inside as long as there are no lights on inside.
The escape hatch frame was degreased and mounted with caulking onto the wooden rim; follow the same procedure as described before.
What I noticed is which was not possible when I bought the boat is that the actual movable part of the escape hatch can rotate 360 ° this way it is always possible to catch the wind for cooling down on a warm day the forward sleeping cabin.
Last picture of this part of the project shows the installed hatch with some other installed hardware onto the deck including the railings.
Walls in forward and aft cabin replacement
Wall covering replacement forward and aft cabin.
Few years ago when the inside of the boat was taken apart the wall covering panels were removed and taken home and stored in a dry area.
It was known that some parts of the plywood were rotten away but the impression was that the actual wall covering could be used again after properly cleaning.
I have tried several chemicals to clean the vinyl and was partly successful but the biggest issue was that the foam behind the vinyl had been wet and that mold has been growing in the foam.
Even after several years of drying the foam did still smell as well as that on several places the foam was gone or falling apart
Further there were at several places damages to the foam on points which are visible.
Most of the panels in the bow did had water damage and the wood was deteriorated and falling apart.
It was then decided to replace all panels with new wood and new vinyl. To buy the wood is reasonable easy but to get the same type of vinyl was impossible in Holland did find this type of vinyl in the USA but with shipping cost and the amount of vinyl needed it would become to expensive for me. I found an acceptable alternative which is very close to the installed one but without the stitching of the lines, so called rail road tracks.
The first step was to remove all the vinyl from the plywood panels to be able to fabricate the new required plywood panels.
This was not too difficult but a lot of staples needed to be removed and the good thing was that the vinyl foam layer was not glued onto the wood.
New marine plywood was bought same thickness otherwise in the aft cabin it would not fit into the slots of the wood.
The plywood was painted both sides to protect the wood for future moisture .
The old panels were drawn onto the new panels and the panels were cut out, the rims of the wood were painted as well.
The next step was to fit the new panels in the boat to see if there were any mistakes made during copying from the old removed panels, bearing in mind the thickness of the to be installed vinyl onto the panels.
It was decided with the supplier of the vinyl to glue the vinyl onto the wooden panels.
Cutting the vinyl is not that simple a good pair of scissors will do the trick but placing the vinyl onto the wood especially where two panels meet each other is more challenging especially in the bow where, the panels are not square shaped.
The panel was positioned onto the vinyl keeping in mind the required overhang to be able to fold the vinyl around the wood and having enough material left to fix it onto the wood.
To make sure that the vinyl lines would follow the required pattern and no changes would be made to the position during the gluing of the vinyl onto the wood the first part of the vinyl around 10 cm was glued onto the wood.
When this was dry, next day the rest of the vinyl was glued onto the wood.
.
Another day of waiting before the material could be folded around the wood and be fixed in position
To be able to glue the material which needed to be folded the area which needed to be glued was left open while the area where no glue should be was protected, I uses spray glue specific for this material.
When one folds the vinyl at the corners a thick part of vinyl will be the result which will be thicker than the rest of the fold over vinyl this will result that the corners will be thicker than the rest of the panels and when mounting them this will be visible.
Therefore at the corners the foam layer of the vinyl was removed.
When both sides were glued in position the corner needed to be glued in position.
We placed very thin double sided tape on the wood and positioned the material in the right position, then one side was folded into the correct position and fixed with staples. The next step was to fix the other side in position and fix with staples as well.
Although a difference can be seen between old and new panels I do think is is a major improvement.
Original the panels were fixed with a brass nail onto the boat I decided to fix them with a screw this way it will always be possible to have them relatively easy removed without damaging them.
The aft cabin is where the aft two panels are placed into a groove between two pieces of wood therefore it is important to keep the panels at the corners as thin as possible.
The following pictures are from the finished installation
Forward cabin before
Forward cabin after installing the new panels in position.
Forward cabin finished overview pictures
Aft cabin before new panels are installed.
Aft cabin after the new panels have been installed.
Installation of Deck hardware
In my case the first part was to go through old pictures with measurements to where to install the re-chromed hard ware.
Pictures are from different installed pieces of hardware.
The measurements were placed on the deck and it was rechecked if the items were in the correct position from center line and forward or aft.
Next it was checked if the holes for the mounting would end up in the supports installed under decks.
Although this is somewhat time consuming it was god that I did do this otherwise one of the holes would have ended up very close to the edge of the wooden support under decks.
The holes in the deck were drilled first small pilot drill to recheck the correct position, followed by the largest drill for the drill for housing the bottom part of the deck bolder, than the last drill slightly larger than the thread size.
The deck bolder was fitted to check for a flush mounting, needed to take some small pieces of wood away to get a flush mounting, the deck bolder is made from cast bronze and are not 100% smooth at the bottom side.
The holes were cleaned and protected with epoxy to prevent water ingress in the future.
The bolder was than place din position and carefully tape placed onto the deck around the foot of the bolder.
Tape was also placed onto the bolder itself to prevent that caulking would get all over chrome parts.
Seal and Glue caulking was added to the bottom of the bolder as well as into the holes in the deck, I used far more caulking than would be required but I rather waste some caulking than having the chance that a tiny hole in the caulking will create future issues.
The nuts were tightened to fix the bolder into place and as can be seen from the pictures a lot of caulking is pressed out between the deck bolder and the deck.
The excessive amount of caulking was removed directly; do not let the caulking become dry out.
Then the tape was removed pulling it away from the deck bolder, this way pre=venting that caulking would end up onto the chrome or onto the deck.
As can be seen from the next picture one has then a clean deck with minimum caulking between the chrome parts and the deck.
Following picture is from the installed bolder seen from the aft side.
Bow before with Painted chrome parts.
Bow after installation of re-chromed parts.
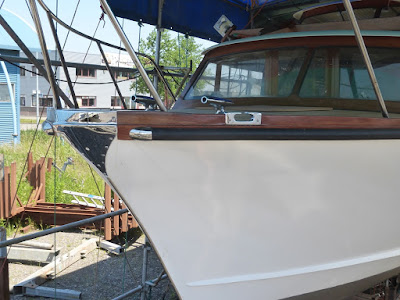
Propeller Shaft
Although a long time ago removed it was time to install again the propeller shafts and fix it to the engine coupling.
At the position where the propeller shaft enters the boat gave me the impression that there were issues with this part due to extra screws added into the wood. Also no gasket could be found between the shaft support and the hull.
The old bolt and nuts were removed and it was clear to me that there must have been water ingress into the boat, they were completely corroded.
These were still the original bronze bolts and nuts.
Everything was removed and the area completely cleaned from any debris, condition of the wood was checked.
As one can see from the next picture there is wasted wood and the condition could be better. Since the boat is this long ashore and has dried out completely, gaps between the planks, I decided not to change the wood in this area, due to the fact that I might end up with an issue when the boat is put in the water. For example if the new wood is wider than the removed wood the gap between the planks might not close.
The plan is now that after one or two years in the water the wood in this area of both propeller shaft penetrations will be replaced.
The penetration through the hull was protected with several layers of anti-fouling paint from inside out as well as from the outside.
The holes not needed anymore for fixing the hull penetration were closed with plugs.
The actual bronze propeller shaft hull penetrations were fully cleaned and sanded to remove any dirt or high spots.
Thin rubber sheeting was placed over the bronze piece and with a round hammer the contour of the bronze was taken over onto the rubber. One has to make sure that the rubber does not move during this process also the holes although not seen on the pictures are marked as well.
Next step was to prepare the new bolts and nuts.
It was decided to use stainless steel bolts and nuts and make them flush with the hull.
Actually threaded rods were made on the correct seize and the nuts were on one side fixed with thread lock, to prevent them from moving.
A small recess round was made in the hull at the positions where the nut would be positioned.
The threaded with nut rod was fitted with washer and small O-ring, to prevent as much as possible water ingress in the hole for the threaded part.
Before installing the fixing bolt it was protected with Sikaflex also to fill the hole where the bolt passes through with protective material.
The bolt was inserted by rotating the bolt by the nut to make sure that all the wood inside would be covered with Sikaflex.
It was made sure that all extra Sikaflex was removed from around the nut and the hole where the nut would fit in.
When the nut was pushed the last few mm at the same time two component epoxy filler was added around the nut and over the nut making it almost flush with the hull.
The nut and thread are now completely sealed from the water, while at the same time the nut is fixed in place giving me the opportunity when the boat is in the water and the wood expands to tighten the nuts on the inside when required.
Nuts are now only slightly tightened.
On the inside two extra holes were drilled in the bronze hull shaft penetration on the aft side to make sure that the whole unit would be flat on the surface and still be tight in place.
This way I do not require to tighten the bolts and nuts to much until the wood is expanded when the boat is placed in the water.
On the inside the stuffing box did get new packing as well as that when the shaft was connected to the engine that the rubbers of the couplings were replaced.
As described with the rudder stock the packing was cut with an angle to get a good connection between the ends so preventing that water would go through and one needs to tighten the stuffing box too much.
June 2017
Floor Steering Cabin
The floor of the steering cabin looked from the beginning not up to my expectations as well as that some of the wood was damaged and a part was rotten in the corner of the deck drain.
I had some teak left over from the installation of the teak deck as well as some Birch for placing between the teak planks.
As can be seen from the next picture the repairs to the boat also did not add positive to the condition of the floor.
First step was to remove the wood placed on top of the ply wood which was the original floor of the steering cabin.
This wood small pieces was glued onto the ply wood and while removing it some of the plywood was damaged as well while some other parts cam off very easy.
The wood was removed hatch per hatch, at the same time inspecting the conditions of the hatches, good news was that the plywood and the rest of the construction of the hatches were in a good condition, most likely due to the position in the boat, above the engine room, warm and dry.
Eventually the whole floor looked like a plywood floor, interesting concept for a fl
oor in a boat.
When all the wood was removed and the wood on the site of the hatches it was noticed that there were screw holes in the hatches which gives me the impression that the original floor has been one with rubber mats and brass rims around the hatches.
One of the reasons that the wood was removed on the site of the hatches was that the hatches did not line up which I did not like and wanted to improve. As can be seen from the next picture with the removed wooden strips on the site of the hatches rather large gaps were created,
New Hardwood strip were glued onto the hatches and the hatches were modified as much as possible to get better lines in the floor of the hatched when installed. As can be seen from the next picture some of the hatches were not cut straight resulting that they needed to be modified. Left hatch with the new rims on the side while the right hatch did still have the old rim.
Next picture as well shows the difference in the hatches between length and width where they should have been exactly the same.
Right hand bottom corner with the new strip on the side of the hatch.
The first step in the finishing of the hatches with new teak was to install on all hatches the wooden piece on the side of the hatches while aiming that all lines would match up, more or less t\hatches of the same seize having the same outside diameter.
The following step was to cut the teak on the right length as well as the birch pieces between the teak. all was installed dry to find a way that at the end all lines would match up in the floor, except of the small hatch in front of the doors of the aft cabin, since this would make the teak on this small hatch look strange due to a few very small pieces of teak.
The plywood hatch was covered in epoxy glue which was colored close to the color of the teak, this to make sure that if the glue was coming out between the planks that it would not stick out as white epoxy glue. The teak planks and birch strips were placed in the exact same as dry fitted and laid next to the epoxy covered hatch to make sure that they would be fitted in the same position as dry fitted.
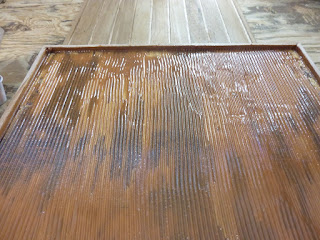
The hatch was covered with 100% epoxy with a toothed cam to make sure that the teak planks could be pushed into the glue as well as that with a toothed cam an equal layer of glue is applied
First two hatches finished and as can be seen some colored glue has been added on top to close any gaps if they are between the teak and the birch strips. This is not an issue since the hatches needed to be sanded to end up with a flush floor, Teak planks were made with the help of a circular saw and were not all exactly the same thickness. Although not easy to notice from the below picture the new hard wood trim pieces on the side of the hatches were kept higher than the actual thickness of the glue and the teak planks, this to come to a smooth hatch in the end.
Some of the planks needed to get cut in the length to be able to fit as closing plank on a hatch.
To make sure that the closing plank would have a tight fit the other planks were put in position with small pegs to push them hard against each other and the rims of the hatch.
Then the plank which needed to be cut in the length was marked with a sharp pencil where it needed to be cut, as can be seen two strokes of birch were placed to make sure that the correct with of the plank would remain after the cutting of the plank.
Slowly and diligent continuing the installation of the teak planks the floor started to show the way I wanted to have it as an end product, this type of work requires quite some time and one should not expect that this type of work is completed in a day or two.
Eventually the whole floor was completed and sanded flush not only each hatch but also between the hatches themselves . As can be seen although not 100% perfect the lines between the hatches do line up much better than before I started with this upgrade.
After the sanding and cleaning the hatches were not varnished but covered in several layers with oil , in my case I used Owatrol Deks D-1, not D-2 since this will make the deck slippery when wet
As can be seen a the teak directly does get its color after applying a single layer.
After the floor was in one layer of oil the hatches were finished with installing the rings for lifting them, also here time was taken to place them in such a way that the hatch could be lifted at one side in the middle while ate the other side they would line up.
In the end the deck in the steering cabin looked as one would expect from an old wooden classic boat,
The one thing left was to place sound insulation at the inside of the hatches , I placed not only sound insulation but also sound absorption.
Repainting the outside roofs
I was under the impression that a light sanding and putting a new layer of epoxy paint would be sufficient on the fiber glass roofs of the main cabin and the steering cabin.
Unfortunately i found out that over the years in my opinion incorrect paint was used for the polyester roofs of the boat, which resulted that I needed to sand the complete roofs till reached the polyester.
One of the first things was t o remove the hand rails on top of the roofs, since I was alone and the threaded rod with nut was going through the roof of the main cabin I used a small trick by taping a screw driver to the round holding bar and unscrew the nut from the inside.
.
With the hand rails removed which were as it looked at the beginning in a bad state, I was able to sand the complete roof.
The handrails were sanded, were painted as well, and after the sanding the the round bars and the support blocks on the roof were actually in a good state no rot nor really damaged. So instead of making new ones I covered them in Owatrol D-1 and D-2 oil as future protection against the weather.
The roof was sanded holes and deep scratches were filled with epoxy filler and and painted with two component epoxy paint and afterwards sanded and polished to get a smooth surface .
The next step was to place the painted handrails back onto the roof.
The support blocks for the round handrail were placed onto the roof in silicone kit, seal and glue to prevent that there will be water ingress along the bolts where the handrails are mounted onto the roof.
This boat the mast is not placed on top of the steering cabin but on top of the main cabin. A new connecting piece was made for the power supply to the horn, and lights in the mast.
Finished roof with an opening for the ventilation in the forward sleeping cabin, fan not installed yet on this picture.
Next roof was the roof of the steering cabin same procedure was followed with paint removing closing the holes and scratches with with epoxy filler and then sanding and painting with two component epoxy paint.
Hand rails were removed as well and in his case new support blocks were made for the round hand rail since they were in a bad state, the blocks were made from mahogany. All was protected againa with Owatrol D-1 and D-2.
Finished roof
The roof for the aft cabin was completely cleaned and stripped from paint with a paint softener but this was a kind of challenging since it does not have a smooth surface.For the sides of this roof which are smooth the same procedure was followed as with the other roofs only here lots of more holes to be closed.
It was then painted with the earlier mentioned paint a thin layer as possible to keep the fish grate in the aft deck clearly visible.
The next step was to reinstall the railing poles again with the refurbished hand rails and the re-chromed hardware like corner pieces and hinges.
After the railings were placed, forgot to mark the position of the poles, so it took some time to figure out where each railing pole it's position was. When all was in place the plastic wind breakers were reattached to the railing poles.
Last picture shows the completed installation onto the aft deck.
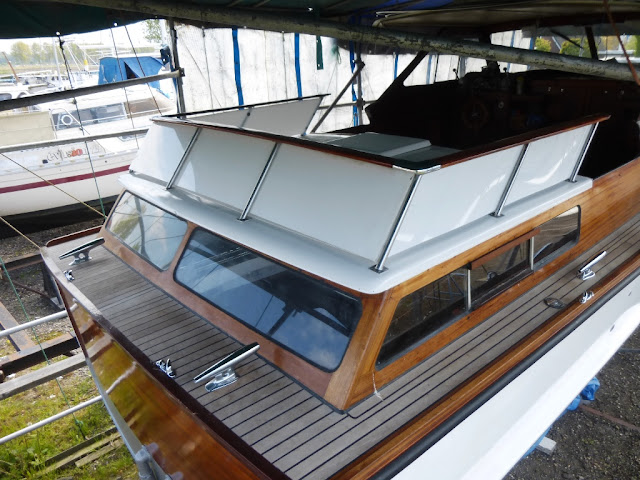
Propeller polishing.
Although a lot of stories from individuals can be found on the internet to not touch the propellers
and especially do not clean or polish them.
One of the explanations is that the propeller can get in unbalance and that it will create damage to the bearings.
Well in case of the Storebro there are no bearings involved in the propeller shaft except the outer bearing which is lubricated by the surrounding water further it is a free shaft which is connected
by a semi flexible coupling to the engine.
Important is of course that the propeller shaft is in line with the outgoing engine shaft.
A smooth and polished propeller can reduce your fuel cost with 3 to 5 %, and with the
old engines I have every liter/gallon is one.
Further a propeller with oxidation creates a rough surface, which not only cavitation can create but also extra noise.
Therefore the decision was taken to clean and polish the propellers.
Although difficult to see from attached picture the surface of the propeller is very rough.
The tools I used for cleaning and polishing the blades is not a metal wire brush or sand paper since I do not want to remove any of the metal of the propeller just the oxidation.
I used for this cleaning nylon brushes which doe very slowly removes the oxidation, this is a slow process but it does remove what needs to be removed in my opinion.
As can be seen from the below picture the propeller is cleaned but still a discoloring can be seen which indicates that I have not polished till the bear metal but just removed the oxidation.
The below picture shows in better detail that the blades are clean and smooth but still some surface roughness can be seen, to remove this one needs to use sand paper or another mechanical means to remove this , which will result in removing metal, what I do not want to do.
At the same time I cleaned the rudders from oxidation no specific reason
but it looks nice for the picture.
Finished product of two cleaned propellers and rudders.
Chain Locker
This is a fancy word for a box, anchor bin, where the anchor chain and rope will be stored in.
The Storebro is not outfitted with a anchor bin for storing the anchor chain.
When I cleaned the the bottom of the boat out I found a lot of sand and dirt which could potentially block the bilge pumps.
Originally the anchor chain just was dropped in the forward part of the forward cabin ending in the bilge of the boat.
Since I did not think this was a good idea and also to keep the bilge clean I decided to build a anchor bin which can hold the anchor chain .
The box was made from water resistant multiplex and inside coated with two component epoxy paint , several layers.
The anchor bin was build in such a way that it had sloped walls to guide the chain to the bottom as well as a hatch was made to be able to check and clean the anchor bin.
Two drains were added to be able to drain the water which might enter the anchor bin.
The Anchor bin had to be installed before the forward bulkhead could be fitted , the unit would not fit through the doors. The Anchor bin is connected to the deck beams with special wood thread bolts.
Although not seen on this picture some additional supports have been added to the bottom of the Anchor bin.
The forward bulkhead was temporarily installed to check if the anchor bin could be reached from the forward cabin for cleaning and inspection.
After installation of the anchor bin the position was decided where the anchor chain could go through the deck. Although originally this entrance is slightly to starboard side from the center line I decided to place the entrance in the center line,
To protect the wood of the deck and sub deck from water ingress the hole for the anchor chain was protected with glass-fiber cloth and epoxy
When finished the deck was de-greased and the wood support for the hawse pipe.
I decided not to place the hawse pipe directly on deck as original but to place it on a wooden support to bring the hawse pipe slightly above the deck this way preventing water entering the anchor bin during a normal rain storm. Further it has now the same installation as the escape hatch on the forward deck
As usual the wood was screwed temporarily in place and then the deck and wood were taped to prevent that caulking would go over the wood which would result in extra cleaning.
Wooden support was removed and the holes for the screws filled with caulking to prevent water ingress which could result in starting to rot the deck while one will not notice this.
Excess of caulking was removed when the wood was screwed in place and at the same time all tape was removed as well.
The next step was to install the Hawse pipe, which is original and has been re-chromed.
The screws seen in the pictures will be shortened when I will install a stainless steel chain to keep the cap of the Hawse pipe near the deck penetration.
Getting Wet
The goal for 2018 is to get the boat in the water.
This might always looks simpler then it actually is, lots of loose ends to be completed which normally always takes longer then one expect.
All wood needs to be sanded from the deck housing and treated again with Owatrol D-2 and in some placed D-1 and D-2.
Deck needs to be washed and checked for any spots which ended-onto the deck by completing other tasks as well as the caulking needs to be checked for agian.
But the biggest challenge is of course when the boat get's wet.
The complete hull has been cleaned inside and protected again with linseed oil and the bilge has been painted.
The planks have dried out over the years and there are big gaps between them, enough to get concerned when the boat get's into the water and how do I keep it afloat.
When the boat does get in this condition in the water it will fill up rather quickly with water resulting that a reasonable pump is required to prevent the boat from sinking.
The risk is that there will be a power outage, pump failure and resulting that the boat still might sink .
Not a pleasant though after all these years of getting it ready.
Thinking outside the box, I decided to fill up the boat with water before I will put it into the water, this way I was hoping that the planks would close again.
Well I was partly successful lots of water poured into the boat which ran out overnight again.
Did this a few times but the gaps would hardly close.
I was then informed about a product called Ettan Grease used by wooden boat builders, it claims that it sticks to anything, indeed it did, difficult to remove from your hands, product is water resistant.
It is a greasy product which smells like tar , old wooden boat smell, not unpleasant.
The good thing of this product that it can be rather easy pushed between the planks, if the weather is not to cold .
Well after putting this Ettan Grease between the planks I filled up the boat again, and to my pleasant surprise only some drips of water came out which could be easily closed with some additional Ettan Grease.
Over the time a week to several weeks I could see that the gaps between the planks were closing.
The Ettan grease was pushed out between the planks and could be scraped off the bottom.
It total took around 4 months till all gaps were closed and no water came out of the bottom anymore.
It took the longest time for the hull shaft penetrations to close which can be expected due to the way this penetration is build up from different types of wood in different layers.
It took some time after before the boat went into the water , I had the impression that most of the planks were closed and minimum gaps were left in the boat by June.
The hot summer after June did not help as planks below and above the water line were opening again.
Another issue was to find a suitable name for the boat, since the boat originates from Sweden we came up with the name Lycka, which means luck and still sound lie a ladies name for us Dutch.
Into the Water
Eventually I waited till the end of August till the board was put into the water.
The height of the tent which served me over the last few years of restoration was just high enough that the boat could be moved out with a boat lift, without taking the whole construction down.
It is always a kind of scary moment when the boat hits the water after being so long on land and have been totally dried out.
But the good news was that it floated directly with a minimum of water ingress between some planks.
This was the first day.
The first 24 hours about 7 liters of water entered the boat actually it would have been more expected if I did not seal some of the hairline openings between some planks, where water was coming through, on places where one would not expect this.
Did a test run with the boat the next day to make sure that there were no issues with the engines steering etc. before the boat would be sailed over from the wharf to the maria and the food news was that boat sailed as expected and no extra water did enter.
Few days later the boat was sailed from the wharf to the marina where the boat will be for the summer and winter season.
The marina is at the big lake in the middle of Holland and the wharf is at one of the canals so we needed to go through locks with a height difference of about 18 feet.
From there over the lake to the marina.
After sailing over all did look good with minimum extra leaking of water into the boat, but I think the sailing and movement did some settlement of the boat and the next day we had far more water in the boat even up to almost 30 liters in one day.
Most of this water came through the blocks, Port and starboard, where the propeller shafts supports are mounted onto.
These gaps were closed with the Ettan grease and this stopped the large ingress of the water.
After about two weeks the water ingress is decreased to around 2 liters per 24 hours , which shows that it takes longer then one hopes that a wooden boat will get water tight, all gaps between planks 100% closed.
Below some pictures of the boat at the Marina.
Since the sea trial was done without major issues we decided to make it official and the boat was christened with some champagne which pored over the bow for good luck.
In a later stage I will follow up with additional blogs with regards to work performed on the boat as well as with pictures of the finished inside.
Not only the inside was restored but also new beds new siting cushions as well as a new tent was made.
The tent and cushion where made by my neighbor Jan who can do miracles with a sawing machine.
Inside lights
During the last years of restoring the boat and when all was accessible the electrical wiring was inspected at the same time.
During these inspections I came to the conclusion that hardly any wiring needed to be exchanged, did not find any discolored copper wires in the cabling nor was the outside of the cabling damaged, therefore a minor amount of new cables needed to be pulled for the lights, in the most cases new to be installed lighting.
With regards to the cabling for the batteries and cables around the engines most of them were replaced.
One of the reason to replace them was to install main fuses which are not a part of the original design of the boat. Other reason was that I wanted to use silicone cables which are no as stiff as normal battery cables and which are easier to install.
With regard to the lights are were replaced except a few in good condition the round ceiling lights in the most forward and aft cabin.
Aft Cabin
In the aft cabin new lights were installed as bed/reading lights.
These light fixtures were fitted with LED lamps to reduce the power consumption, as with most lights installed where possible the halogen lamps were replaced by LED lamps.
The storage shelf port and starboard looked a bit dark to me and since I was running several new wires I installed LED strips to make the shelf more visible and at the same time create some more light in the aft cabin.
The aft cabin storage cabinet was a kind of dark to my onion and since I had some LED strip left and switches a part of the LED strip was installed in the cabinet.
The LED strip is relatively cheap and when one looks on the internet one can buy rolls of 10 meter, 20 meter or even longer. The advantage of these led strips is that they can be cut to length and directly be connected to the 12 volt circuit no additional transformer or anything else is required.
Original ceiling light as far as I know.
Main Cabin
What I noticed that with the original light the main cabin is rather dark therefore some additional light have been added. When I bough the boat the center round light was removed and replaced by some smaller lights which in my opinion did not looked that nice.
A new concept was made from Mahogany with 3 individual lights which now do give more than enough light around the dining table.
Other lights were on the walls when I bought the boat but in my opinion not positioned in such a way that they would be good reading lights.
Therefore some investment was made and two flexible spots were bough and positioned on the cabinets this way creating lights on the corners of the couch.
The same was done here as in the aft cabin with placing LED strips above the shelf behind the couch cushions.
The space behind the cushions is divided in an aft larger space as per above picture and a smaller forward space behind the small back cushion.
Since we have these days all telephones etc. which need to be charged through an USB behind this smaller cushion I placed USB ports for charging, as well as a lighter outlet for any other connection and a volt meter showing the voltage of the house battery.
For the kitchen area a light was placed on the wall above the sink and the original light above the stove was left in place.
The kitchen cabinets looked a bit dark as well and with keeping in mind all what I found when taking the kitchen area apart I thought it was a good idea to place also LED strips in the storage cabinets.
The larger storage cabinet next to the couch was also outfitted with a small light which becomes very handy since this cabinet is rather deep.
The bathroom has only one light which I did not changed since it is a fluorescent light which gives enough light for a bathroom.
Forward cabin, bedroom.
The original round ceiling light was kept in place to keep the boat as original as possible.
new bed light were installed against the cabinets in the forward cabin.
Bit classic look to try to match it with the age of the boat.
These lights do give more then a enough light for reading and checking the cabin in the dark if required.
In the port side larger cabinet was also a LED strip placed, in the small starboard side cabinet this was not done since it is so small that the light would not have any effect.
Further also here two USB ports were installed for charging.
Original ceiling light as far as I know, next to the ceiling light a small fan which works on solar power which I hope will create some circulation while the boat remains in the water during the winter months.
\
Steering Cabin.
In the steering cabin one larger light is positioned between the window wipers this way when one is docked or at anchor giving enough light in this area to move around without tripping.
Also here on the right hand of the console an outlet has been made for 12 volt, this allows for plugging in for example a navigation computer.
What I noticed was that the cabinet which holds all fuses was a kind of dark and especially when one needs to replace a fuse, which always can be done with a flash light in the dark but it is nice to have two hands free when changing a fuse.
Also here a LED strip was placed with a switch which activates the light when the doors are opened.
Sometimes I do get the question why keeping the old fuse system in place and not replace it with a more modern system.
One of the reason is that I wanted to restore and not rebuild the boat to as much as possible original condition the other one is that changing the amount of fuses to a new system would require more space and would become a kind of expensive.
The good part of the present system with this large amount of fuses is that the electrical system is set up in such a way that when a fuse blow that non of the cabins will be totally in the dark, which I think due to my work on board on ships is a major advantage.
For example there is one fuse for the port side aft bed light and starboard forward bed light, so if his fuse fails there will be still light in both areas.
Main Electrical system.
As with many older boats, cars etc. owners are modifying and running over the years new cables for their own purpose but in some cases this becomes a hasty job, especially when the cables are not in sight and this can result in not proper guiding of the newly installed wires/cables.
I understand that we are working with low voltage but still in case of failures blown fuses it is important that cable runs can be followed, especially with the battery cables which will have a high amperage in a short circuit.
With the above in mind you already understand that I did not found the boat up to my standards.
From below pictures it can be seen that loose wires although connected were hanging around in the engine room spaces and fuse cabinet. Additional, battery cables were not seized correctly.
First attempt was made in removing the wires which were in my opinion obsolete and could be removed without jeopardizing the original installation. This was done around the batteries and in the fuse cabinet, this took some time but the result was that all looked already better.
To be honest I have done this several times with the cables around the batteries, also due to changing the position of the batteries in the engine-room space.
Eventually the final version was installed.
For example the main switches for the battery system were placed under the small hatch aft of the steering cabin near the doors of the aft cabin in the engine room space, long cables runs especially since the batteries were placed ports side under the steering console.
Moved the switches forward under the floor but that was not ideal.
Therefore I made a small cabinet next to the steering console where these switches were placed in.
Short cables between the batteries and steering console.
The batteries were place in between the engines in line forward to aft and I invested in Optima batteries as starting batteries and an additional house battery.
What I noticed was that each engine it's alternator was connected to one battery with no regulating system to check which battery was empty or full.
I therefore invested in a regulator which is fed by both engine alternators and checks which battery is the lowest in amperage, first starting to load the starting batteries before the house battery, also this unit was placed in the new cabinet.
This unit can feed 4 batteries but for the moment I have connected 3 batteries; two starting batteries and one house battery, of which one start battery can also be connected as house battery to the electrical system, while the other one is solely a start battery. This way I should always be able to start one engine.
Further with this unit it gives me the opportunity to sail low speed with one engine on line while at the same time charging all batteries.
Picture of cabinet with charger unit and main switches.
The above picture shows also a charger for solar panels although old solar panels they still do charge the house battery.
The main electrical system was not fitted with main fuses between the batteries and the ships electrical system, therefore main fuses were installed as close as possible near the batteries.
With the changes by installing the charging unit, fuses and main switches the amount of cables increased but by using silicone cables the cable runs were not that difficult. Although it looks from below pictures a lot of cables.
The fuse cabinet was cleaned up as well light added and the fuse covers were marked with the fuse position behind the covers this way when a fuse blows it can be quickly replaced.
Inside Pictures..
Although one never is finished with restoring an old boat and the small items takes the longest time to complete, I would like to share some pictures of the completed inside of the boat.
In the bow new mattresses were made with special covering for boats which are anti allergic and resistant against mildew.
The bottom of the mattress was covered in an open structure to be able for the mattress breath and not hold humidity in them. This was done for all mattresses and cushions in the boat.
Although with the above knowledge and keeping the boat in the winter in the water the mattresses and cushions have been removed.
New mattresses were bought, the foam and my neighbor was able to cover them.
Foe the new foam the old mattresses were used as template which came out very well, everything fitted tight as it should be no large gaps.
This method works better in my opinion then making templates for example from carton.
The forward bulkhead was renewed as well in the restoration process but the doors to the anchor bin are the original doors.
The Main cabin kitchen as mentioned in one of the blogs was taken completely apart sanded and re-varnished. The sliding doors of the cabinets are original and were just cleaned, they are still in a good condition.
I kept the original cutting boards in place. New faucets were installed as well as new potable water lines from tank to the faucets in the kitchen area and bathroom.
The storage area for plates and cups was taken apart again since the present seize of cups and plates did not fit in the spaces for them, some minor new arrangements were made with the vertical supports and all fits now as it should be.
When I bought the boat there was no cover over the stove, old fashioned Taylor cooker which actually works well, and since this did not looked good as can be seen from the following picture a cover was made and placed over the stove, cover can be seen in earlier pictures.
Below picture shows the stove in view
The dining table which I think is not original was varnished and new wood pieces placed on the side to prevent that when the boat list slightly all is sliding of the table.,
.
Also here in the sitting area the cushions were 100 % renewed as well as the aft wood support to the back cushions which was painted as well to protect the wood from humidity.
Original this was not done and the wood support for the cushions was unpainted.
Since this Storebro 34 is a Deluxe Storebro we do not have a U-Couch but an L-couch with at the end a closet and a so called Captains chair.
This captains chair was completely stripped and re varnished after the wood was stained with a color close to mahogany. Comes out always more red than one hopes for.
The bathroom which also can be used as a shower area was as mentioned in an earlier blog completely stripped and re varnished in a two component epoxy varnish to withstand water in case we are planning to take a shower here, which for sure at this moment is not in the planning.
The original toilet was removed, since it is not allowed in the Netherlands to discharge black water in inland waters, therefore a chemical toilet was installed which actually sits nice and high.
On the right upper side one can see a gauge and two switched, the gauge is for checking the water level in the potable water tanks which is switch activated while the other switch is for the potable water pump which stops when a certain pressure is reached, a pressure vessel for potable water is installed in the engine room spaces.
The aft cabin same as in the forward cabin the mattresses of the beds were completely renewed.
Further all wood work was sanded and re varnished as described in earlier blogs.
The steering area as described in earlier blogs was also completely sanded wood replaced where required and varnished.
The steering stand was kept original no changes in gauges or switches just wood sanded and material around the gauges cleaned and polished.
The foot supports, port side and starboard side were installed again, although I'm pretty tall one never knows when one needs them again.
The chairs, as far as I know original were re-upholstered and we choose for white seat, do not know if this is original but I think it looks nice with the wood in he steering area.
Sea Water Cooling Pump
After the boat went into the water and all overboard valves were checked as well as hose connections, the mud boxes were filled up and before the engines were started ,to prevent that the sea water pump would run to long dry, although prepared with acid free Vaseline, I filled up the pump with water through one of the plugs above the pump.
With one engine there was not issue but the other engine the water ran straight out of the pump through the mechanical seal.
Although I'm familiar with these type of pumps they are not all the same and especially the older pumps from around 1970 are not the same as build as these days.
To know which pump type was installed on the engine, engine manual does not informs you which pump actually is installed, I had to remove some paint from the cover and was able to check for the correct type. The one installed on my engines is a 1" type of pump.
I was a kind of lucky to find this information since from the other pump the original cover was removed and replaced by a stainless steel cover.
Going through the internet to find the correct drawing, which took me some time I found a Johnson manual with drawings and spare part numbers.
Going through this manual I also noticed that quite some parts are not available anymore which created some concerns from mys side, since I expected that the mechanical seal was broken.
The found drawing in the manual gave me an better idea how the pump was build together.
See below drawing.
Taking the pump apart after having removed the pump from the engine I directly noticed that the circlip , part of position 4, was not installed therefore preventing the mechanical seal rotating part being pushed against the stationary part.
As can be seen from the next picture of the other engines sea water pump the cir-clip is clearly visible.
To be able to run the engine and not filling up the bilges a rubber O-ring was placed between the housing and the stationary part of the mechanical seal and by installing the impeller the mechanical seal was compressed and in such way there was no leakage, although I know this is not the correct way of repairs it fits it purpose and in the man time I was able to search the internet for the correct parts.,
The idea was to completely overhaul the pump and replace all wear and tear parts, items 2, 4, 6, 8 on the drawing. Reason was that I have no idea how many running hours the pumps do have and if they are still able to give enough cooling water to the engines on long runs.
There the challenge started as I could not find any company in Holland who as able to supply all parts I required.and I ended up in the USA with a company who was able to supply all required parts.
After the new parts were received the first step was to remove the pump again from the engine and check the condition of the pump shaft to see if there was an issue to install the circlip. As can be seen from the below picture the groove for the circlip to keep the mechanical seal in place was completely filled with rust, most likely an incorrect type of material was used for the circlip when the last overhaul was performed.
After cleaning the rust and debris out of the shaft the groove became visible again.
The next step was to check if the circlip would fit in the groove and would remain in position after being installed, this was the case and the circlip was removed again.
The following step was to take the pump further apart and to check the dimensions of the old parts and the new parts, the wear might be less than I would expect and there might be no need to exchange the parts and safe the new parts for the future.
The cover as can be seen from the picture showed quite some wear actually the thickness of the old cover was 2.2 mm while the new cover is 2.5 mm.
The covers was replaced on both pumps.
The next part which was removed was part No. 2 the guidance piece for the impeller, it's simple to remove just unscrewing from outside.
On both pumps this part was not stuck. Checking the measurements at the thickest part I noticed quite some wear, old one 4.5 mm new one 6.3 mm and this was a good reason to replace this part on both pumps. On the picture this wear is also quite visible.
I do not think that this wear will reduce the capacity of the pump since the impeller will still be able to close the suction from discharge side.
The next part which was changed was item 8 the bottom wear plate where the impeller runs over.
The plate removed was 1.7 mm and the new plate 1.8 mm not much wear but one could see the area where the impeller had ran over.
The mechanical seals were inspected and I could not see any damage to the running surface nor excessive wear and therefore they were reinstalled and not replaced.
What I noticed that when i put all new parts in the pump housing that item 2 was slightly sticking out above the surface of the pump housing. This was solved by cleaning the bottom surface of the pump housing since over the years time some debris and corrosion had been building up preventing that the bottom wear plate item 8 could be completely going in its place.
Below picture shows all new parts installed including the ring between circlip and mechanical seal which was not found when taking the pump apart, might be that at earlier overhauls this ring was not installed but according to the drawing it is a part of the pump and therefore I did install the ring.
Pump installed on the engine and the circlip installed on the shaft, this went relatively easy and therefore I think that the ring between circlip and mechanical seal is a part of the original installation of this pump. The circlip is not from steel or stainless steel but from brass , therefore it does not stick out on the below picture, but can be seen.
The pump was further build together impeller installed and new cover with new screws completed the overhaul . A test run was done with the engine and although difficult to see it looks like that some more cooling water is running through the engine and I also have the impression that the pressure is a bit higher.
Installation Hydraulic steering unit
During the reconstruction of the boat it was noticed that steering was rather heavy.
Checking the route of the steering cables nothing out of the ordinary could be found.
The steering cables were as good as possible cleaned lubricated etc. in the expectations that over time the steering would become more easier.
It was also during the construction period checked if the actual steering unit connected to the steering wheel could be taken apart but this looked not that easy as one would expect and was left as it is at that time.
While sailing with the boat it was noticed that there was no improvement in steering the boat, no real issues to keep the boat on track but the actual steering was still rather heavy and not that easy while maneuvering, although this could be compensated with both engines.
Since I was not satisfied with the situation it was checked if there would be anything incorrect with the rudders, cables were removed from the rudder arms but there was no improvement in rotating the steering wheel. Rudders could be moved freely.
Next step was to take the steering unit apart but unfortunately I was not able to do so.
Removing all bolts and nuts was no issue but splitting the actual unit to reach the cables was not possible, without most likely damaging the unit.
I expect that the reason for not being able to open the unit is not only the age of the system but the cotter pins installed in the unit, see below pictures.
With this issue it was decided to look into a new steering unit with new cables, going through the internet for additional information and cost it was clear to me that there was not a lot of price difference between the cable system, complete unit and a hydraulic steering system.
It was then decided to switch from cable steering to hydraulic steering.
The original cable steering was removed and looking at the inner cable in the outer cable I could see that all was rusted, this was also mentioned on the internet in several websites that when the steering becomes heavy most likely the cables are rusted and that there is a great chance of a cable failure.
After the old steering unit and cables were removed the new hydraulic steering was installed.
Cabinet in the aft cabin was removed and position of the new plunger was checked that it would fit within the space available.
At this point I made a mistake, by counting the revolutions of the steering wheel hard starboard to hard port and comparing this to the instruction manual of he new steering unit, both were about the same amount of turns from hard port to hard starboard.
Therefore I was under the impression that I could use the same connection as where the original cables were connected.
A new support frame was made to fit the plunger and all looked as it would fit and work without any issues.
Reading the instruction manual more precise I noticed that instead of 35° rudder port and starboard I most likely would reach half of that steering angle.
New plan was made and the complete steering angle was drawn on carton and measured from the center line of the rudder stock with the information available in the instruction manual.
It became then clear that the original connection for the steering unit would not be the correct position of the connection to the hydraulic plunger.
A new hole was made in the rudder arm for the connection to the plunger.
From below picture it can be clearly seen the plunger stroke for full rudder movement between 35° port to starboard, Red line new position of the plunger stroke for full rudder movement.
Blue line if the plunger would be connected to the original position of the rudder arm.
This new position of the plunger resulted that a new hole needed to be made in the rudder arm, since this is brass it can be done without removing the rudder arm from the rudder, in my case this would not be possible since the boat is in the water.
Not only I made a new hole but I threaded the hole this to make sure that when the plunger would be connected that the rudder arm that it would have the less chance to get loose even under vibrations.
The hydraulic plunger was connected with a bolt and locking nut.
A new support was made for the plunger position and all was put in place before finally mounted.
An additional check was made to make sure that with the plunger stroke full rudder movement was possible.
Hydraulic hoses were ran between the steering pump and the plunger and all was mounted in place.
The hydraulic hoses were both kept at the same length this to prevent any steering delays between moving from port to starboard. Actual length of hydraulic hoses used was 7.5 meter per hose.
For filling the system with hydraulic oil and venting the air out of the system one needs to follow the instructions of the manufacturer.
The hydraulic pump, actual steering unit, was installed in the steering stand and although I had concerns that it would have a large impact on the actual steering stand it does not look to bad.
As can be seen the steering unit does not look that bad on the whole steering stand.
An issue was that the original steering wheel did not fit on the new steering unit.
The original steering wheel has a straight shaft while the new steering unit has a conical shaft, I have considered several option to make it "work" but in the end I ended up with buying a new steering wheel which is actually almost the same as the original one.
As can be seen from above pictures I moved the steering unit slightly up since I'm a tall person, but still there is enough clearance between the steering wheel and the steering stand.
Below old and new
Window shadese
Although we have the boat in our possession for several years we have been looking around for a suitable window shade.
Since this is interior decoration, I'm as a boat repairman less suitable to pick the right type, according to my wife.
We have discussing several options of which one is normal curtains but they will hang loose at the bottom especially at the front windows.
There are tricks of course to mount them in the bottom but we did not see this as the solution we were looking for.
First option was to install plastic window shades the type of small strips hanging from the top on ropes but those are rather wide and only can be used from bottom up.
We ended up with with Blackout Cellular shades, also called in Europe Plisse curtains.
Reason for the black out type is to prevent as much as possible daylight into the cabins to prevent discoloring of the wood as well as to keep the temperature as low as feasible , especially during the summer season. Additional benefit it is rather dark now in the boat in the aft and Main cabin.
As can be seen from the above picture the inside is a kind of aluminium foil, while the outside facing is white and the inside facing is a brown color.
To be able to use the sliding windows the shades were placed in such a way the ones in front of the other fixed windows were mounted against the window frame while the one in front of the sliding window was mounted on the ceiling support and cabin support.
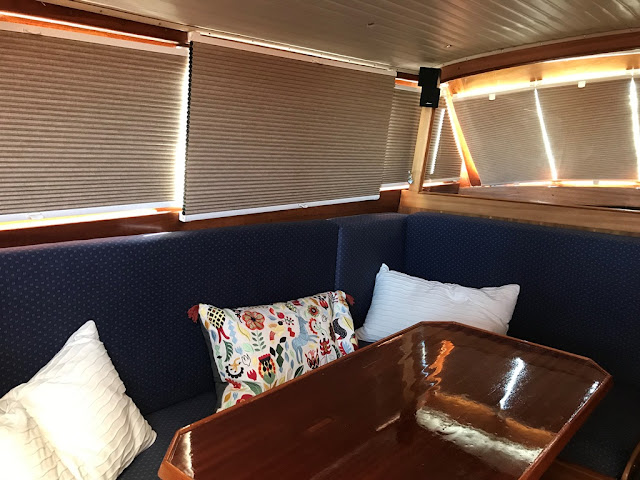
Not only by installing the shades as mentioned above has the advantage that the sliding windows can be operated but also there is some overlap between the different shades which reduces the light coming into the cabins as well.
The shades are installed, ordered , that they can be used both ways so called top down and bottom up.
We are under the impression that this will give us more flexibility with regards to sun and light into the cabin and still have the privacy one sometimes prefers.
As can be seen from above picture top part of the shade is moved downwards .
As can be seen from above picture the bottom of the shade is move upwards.
The shades can of course be moved upwards and they are positioned in such a way that the full window is clear from the shades.
The outside of the shades are white which of course helps in reducing the temperature inside of the boat.
The front window of the main cabin became a challenge since the window is not only curved but is also not the same size comparing middle part and the outside part .
This is of course a result of the curved deck. The idea was to place one or two shades next to each other but making some samples from straight wood it showed that we would lose to much space inside and that the shades would not follow the window as nice as one would prefer.
The above resulted that it was decided to place 3 shades next to each other per window, so in total 6 shades next to each other.
As can be seen these shades are not overlapping but mounted against each other, this give a slight challenge with opening them but if one follows a routine from opening them from inside to outside they will not get damaged.
From outside this looks rather nice.
Kitchen area same principle was used for overlapping both shades .
For the aft cabin the same principle was used as for the main cabin sliding window overlapping the fixed window shade.
The corner window shades , 4 in total in the boat 2 forward and two in the aft cabin can only be top down since this is the only possible way to open them , this is since they are made to follow the window and cabin window frame , but since these are fixed windows I do not see this as an issue.
The shades for the aft cabin were more simpler than the ones fro the main cabin this since the windows are straight windows with only a slight curve in them.
We were able to place two shades next to each other per window.
From the outside this looks natural as well.
Although this is not the cheapest solution we are satisfied with the result , it takes some time to measure how to install the shades and some digging on the internet how they need to be measured and installed but in the end they were delivered ready to install no adjustments required and with good installation instructions.
Propeller shaft seal foundations
Two years ago when the boat went into the water most of the hull became water tight after some weeks , there was only one issue with the wooden foundations where the bronze unit with shaft seal was mounted onto the bottom of the ship. This foundation on both sides kept dripping water and the only way I could stop it was filling the surrounding of the wooden foundations with Etan grease, which actually hold for almost two years without an issue, boat stayed dry. Since I did not see this as a final repair it was decided to remove them inspect them and if required replace them at the moment the boat would be out of the water for the normal underwater works.
With the knowledge I have from this boat it was expected that the wooden foundations would be fixed with screws through the bottom of the ship. When the boat was out of the water the paint was removed around the propellor shaft where it was expected that the screws would be fitted into the hull.
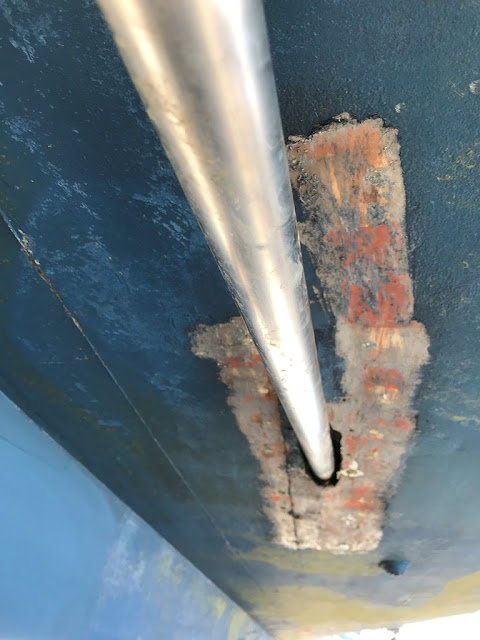
The next step was to remove the screws, first the plug material for the screw was drilled out with a smaller drill the the actual plug seize one need to be care full not damaging the screw head to much since it will then be difficult to get the screw removed, with a little scraping the hole can be cleaned and the screw easy removed .
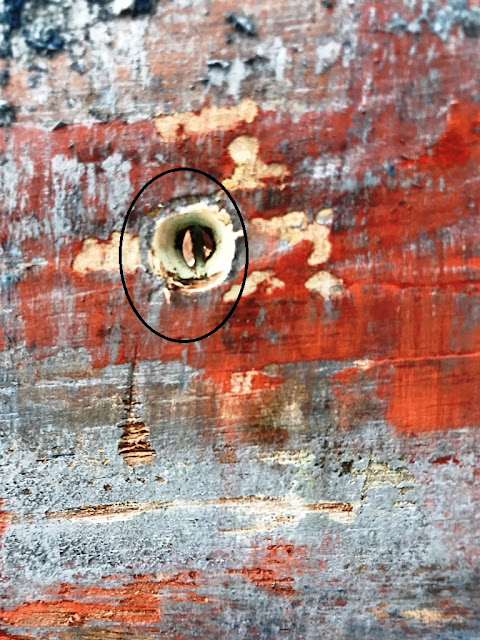
With all the crews out, shaft and the bronze shaft support removed I noticed that I would never get the wooden foundations out.
The reason is that it was impossible to remove the foundations since there are two transversal frames running over the foundations which needed to be removed.
Instead of cutting out the complete frames I removed small sections out of the frames on the forward - and aft side of the foundations.
forward side
Aft Side
With these small sections removed, with the use of a multi tool, I was able to get the wooden supports removed from the ships hull. Although this was not as easy as anticipated. I ended up with cutting the caulking between the different sections with a hack saw blade and a wedge between the support and the ships hull, this way slowly separating the pieces from the hull and each other. Unfortunately I lost the pictures of this removal. It is time consuming and one needs not to rush this task otherwise there is a change that the wood of the hull gets damaged, eventually the caulking will get loose from the wood. One important part is to take measurements of the foundation height on different places to the hull before the actual removal is started this since the supports are not 100% straight in lengthwise direction.
Removed foundation grey area is where the water ingress was
When the foundation were removed one could clearly see that it was build up out of two pieces which were hold together with caulking as well as that the bottom piece of the two was fitted with caulking to the ships hull.
The two pieces together also shows that there has been water ingress between them, those are the grey areas on the pictures, caulking just fell off the wood.
Two pieces on top of each other
One of the reason that the caulking failed could be that the boat has been out of the water for several years and that by drying out of the planks the caulking got loose from the different areas of the hull planks and from each other. Below picture shows areas where the caulking was not attached to the wood.
The parts were cleaned and removed from caulking to be able to take the proper measurements of the wooden pieces as well as further inspection to check if they could be reused.
It is clearly to see from the next picture that the two pieces are shaped under an angle to keep the bronze shaft seal unit horizontal in the boat.
As can be seen from the next picture it was not possible to reuse the removed pieces of foundation some of the wood was deteriorated and had grooves were water would pass through.
The decision was therefore made to make two brand new foundations, instead of using two pieces I planned to make them from one piece. Unfortunately I had not the wood with the right thickness therefore I glued with epoxy two pieces together to get the correct thickness.
Then the part came were the wood needed to be shaped in the right form, first part I used a planing machine .
Then good old manual labor was used to get the pieces under the right angle.
During the shaping of the foundations regular checking was done to see if they are still straight , this is important since if they are not straight/flat they might not fit with the minimum caulking required onto the ships hull.
Before starting with the holes for the propellor shafts the foundations were measured for the correct seize , thickness and sanded to take most of the roughness away.
Next step was to decide where the holes would be positioned in the new foundations for the actual propellor shaft. Center line was drawn on the new foundations and the old one was placed on top of the new one to get an idea of how and where the holes should be made in the new foundations. Blue line is the centerline of the wood and the red line is the approximate oval hole for the propellor shaft. This picture also shows that there were so many holes in the old foundations that it was anyway a good step to replace them.
First a hole was drilled in centerline and approximately center for the opening.
Next the hole was made larger with a reciprocating saw, of course following the lines for the expected opening in the foundation. Lines were drawn on the old and new piece to make sure that the depth of the opening for passing the propellor shaft would be the same as original. This was done on both sides of the wood incoming shaft and outgoing shaft of the foundation.
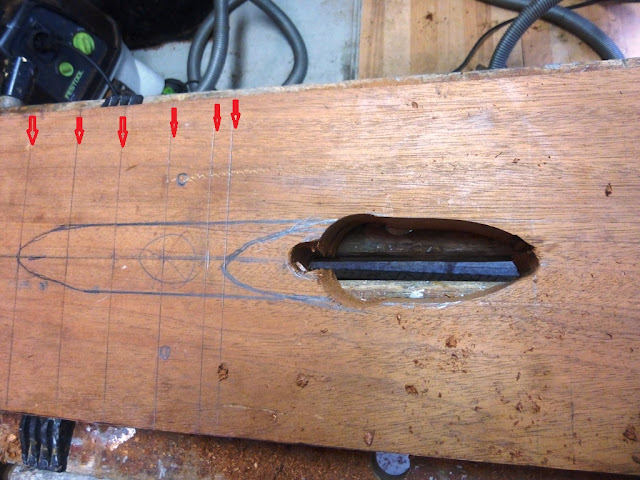
Then old fashioned hand work started with a chisel to create the opening for the propellor shaft. Important part is to mark the foundations well like port and starboard but also top and bottom this since the openings are not the same at the bottom and top side.
Some modern measuring method for checking the depth of the opening.
After the openings are completed on both sides the final thickness of the foundation was completed and it was checked if all was flat .
All was sanded on both sides and ready to be installed in the boat.
Installing in the boat was so called dry installing to see if the propellor shafts would be in the middle of the hole of the foundations as well as that they would not touch the wood. Some adjustments needed to be made to the new foundations, minor sanding .
When al was to my satisfaction the next step was to check if the bronze shaft seal support would be in the correct position. This with the new foundations in place temporarily fixed with a few screws through the hull of the ship. The shaft was temporarily mounted with the coupling onto the engine and it was then checked if the shaft was approximately the middle of of the bronze unit. At this point the bronze unit was fixed in place with 4 screws. In my opinion it is not useful to spent a lot of time to get the shaft exactly in the middle of the shaft seal since the boat is out of the water and although fixed on quite a few supports under the keel and supports under the hull forward and aft the boat will be different in the water
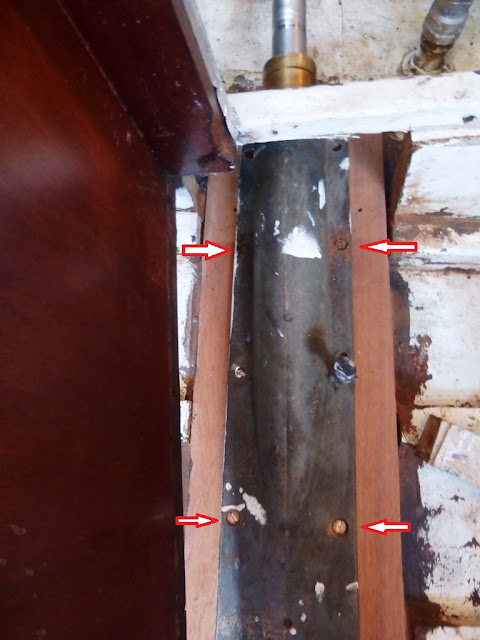
With the unit in fixed position it was now possible to drill the holes through the foundations and hull for the mounting bolts and nuts. Due to space limitations a long drill was required. The good news is that the new holes in the supports ended up in the old holes of the hull planks.
With all prepared for the installation of the foundations the hull and foundations were degreased for final installation. The actual mounting of the foundations was done with caulking for this purpose. I made sure that a thick enough layer was evenly spread out over the fondations to make sure that a 100% seal would be accomplished between the foundation and the hull. The foundations were fixed in place with the screws through the hull from outside. Holes were pre-drilled in the foundations to prevent splitting of the wood.
With the foundations in place they caulking on top was sanded off and they were painted. I noticed that antifouling paint will not dry on caulking therefore I used a commercial wood primer , which does dry on caulking, before using antifouling primer and antifouling paint.
What was noticed at the hull outside was that the holes for the bolts were rather large this was solved by cleaning the holes and installing wooden plugs.
When the glue was cured the holes were drilled through the plugs from the inside and this way I had the exact hole for the bolts I wanted to use.
Next step was to install the bronze shaft seal units with caulking onto the new foundations.
Bolts were installed with caulking around the thread and at the end the whole bottom was cleaned up and treated with anti fouling primer and normal anti fouling paint.
On the inside the removed pieces of wood, from the frames, were glued and screwed back in the same position before the boat went into the water.
Looking at the above picture only thing left is to clean the bronze shaft unit which is a nice job for the winter time.,
After the boat was in the water for a few days and after two test runs the alignment of the shafts was checked and as I expected some adjustments needed to be made, but no leakage around the new foundations.
Sliding windows
Since I wanted to restore the boat and keep it as much as possible original the plan for the windows was to keep the system the same and not installing a new type of window frames.
I have looked around received some samples but in my opinion the aluminium window frames will not look nice with the classic look of the boat, even though one can order them in black for example.
Although the above statement is not totally correct as can be seen in an earlier blog the fixed windows were installed in the frames with a modern suitable window caulking instead of the original design.
For the sliding windows it was decided to stay with the original design which is a silicone sealing where the glass slides alongside and between the chrome guiding strips at the top and bottom of the glass.
After testing different types of clear silicone from the building market I chose one which is used in bathrooms and is UV resistant.
Till so far this works fine, and if it fails, relatively easy to replace.
Since the actual sliding windows always leaked during heavy rainfall and water started to collect at different spots in the boat especially in the aft cabin at the aft side corners, where also a lot of damage was found when I bought the boat, I had to come up with an idea how to stop this water ingress.
Looking around for sliding windows and after a long call with a supplier of sliding windows it was decided to stay with the same system and make some modifications. During the call I learned, statement from a manufacturer, sliding windows almost always leak, the best thing to do is to make sure that the water does not enter the boat, but drains outside.
With this information I decided to find a solution and install a "gutter" around the sliding windows with a drain to the outside.
On the building market I found a hard plastic "gutter" which would be suitable for my windows.
A U-shape hard plastic with a lip.
The lip was cut off to get a U shape "gutter" where the sliding window would be fitted into.
This U shape was the same size as the width of the area where the sliding window was fitted onto.
This would be all fine but the area where the window slides along side the silicone seal it would not be touched and this would create additional water ingress between the U shape gutter and the sliding window, therefore the area where the window touches the silicone seal the material was removed.
Everything was removed the metal strip and the wooden support for the sliding window .
The plastic " gutter" was installed between the wooden support and the metal strip where the window slides over, this way fixing the plastic in place.
The plastic was closed at both ends with a small piece of plastic glued in place while the plastic was glued with silicone at the vertical seals for the sliding window.
At the end of the "gutter" a hole was drilled to the outside to drain the water, aft ships side.
Into this hole an aluminium pipe was placed, the outside diameter of the aluminium pipe had the same seize as the hole I drilled resulting in that the pipe had to be inserted into the hole with some force, this way getting a tight fit, where the pipe stuck through the plastic it was slightly widened to get a good fit with the plastic as well as that at that point glue was used.
To make the windows slide a bit easier alongside the silicone and over the metal rails some silicone grease was added, I hope that over the coming years the silicone and grease become a smoother surface then at this moment resulting that the windows slide a bit easier then at this moment.
As can be sen from the next picture the "gutter" is hardly visible.
For the Vertical sealing of the sliding window I have tried different materials amongst some of the car industry windows, all of them did fail or had in a short time rust particles and algae growth. I ended up with soft rubber hollow material which is normally used to keep a draft out of the house on door frames.
This material was glued in the space of the vertical window frame with super glue the original glue strip was removed from the rubber. When the window is closed it pushes slightly the rubber in creating a good seal against water ingress.
As can be seen from the next picture a little bit of silicone was added to the window frame and glued against the vertical window seal creating a watertight construction.
Till so far after the above installation I have had no water ingress into the boat anymore through the sliding windows in the ship.
Additional I have installed during the construction of the boat rain gutters above the sliding windows to reduce the water which will run from the roofs over the windows a simple L-shape piece of wood which is slightly longer than the sliding windows.
This piece was fitted against the ships hull above the windows and where it overlapped the windows it was glued with silicone caulking.
As can be seen from the next picture the water is now running over the fixed windows instead of the sliding window where it can enter the boat.
2020 Upgrades Trim flaps , Stern Ladder
When the boat was out of the water in August 2020 not only the propellor shaft seal supports were replaced but also some other minor upgrades were installed
When I bought the boat it was outfitted with a Bennet trim flap installation at the time of the restauration I decided not to install the trim flaps one reason was that the switch was broken the other was that I was not planning to drill more holes in the hull.
While sailing with the boat at higher speeds it was noticed that the bow came quite a bit out of the water and the stern was drawn into the water, although this might look nice while sailing the result is that the ships speed does not increase that much while additional fuel is consumed and with the present fuel prices the plan was made to install the trim flaps this time. New switch was bought from Bennet in the USA the whole system was tested before installation , pump and plungers which move the actual flaps and all was found to be leak free and in a good working condition. The actual installation of the trim flaps I will no discribe since this is per manufacturer different and I would be copying their instructions.
During one of the test runs it was noticed that the boat sailed smoother through the water with the trim flaps in use, speed trial I have not performed yet since some yearly maintenance is required on the engines at this moment. The controls for the trim flaps are placed next to the steering wheel while the hydraulic pump is place in the aft cabin under the bed against the engine room bulkhead.
Hydraulic unit.
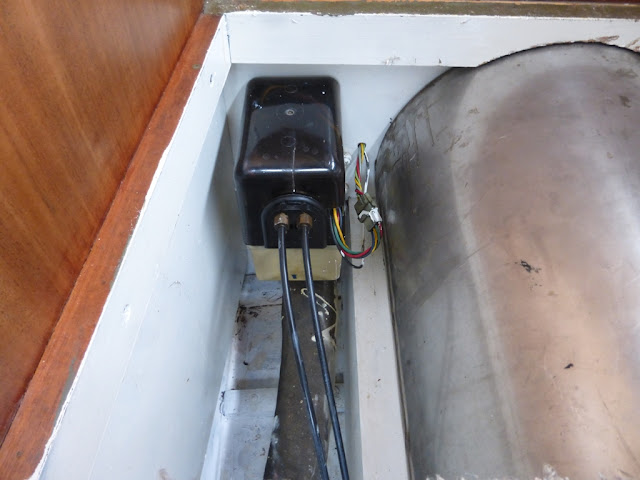
The controls for the trim flaps are positioned next to the steering wheel. Each trim flap can be controlled individually.
The trim flaps were positioned as far as feasible in the direction of the sides of the ship to get the maximum support from them.
Swimming ladder
The dek of the boat is about 1 meter above the water line so when one falls overboard will be very challenging to get back on board. After long discussion with my wife it was decided to install a ladder at the stern of the boat. Herewith started a challenge to get the right ladder which require a certain amount , 3 steps, under the water line. With a height of 1 meter above the water line this was not as simple as one would expect. Eventually we found a ladder with 8 steps from Batsystem which is suitable for our boat.
As can be seen folded out we do have the required 3 steps under the waterline and with the trim flaps moved as far as possible to the outside it will be no issue to get onto the ladder from the water.
Ladder as can be seen is above the water line while the ship is in the water.
Depth/speed Indicator
The , I presume original speed indicator was broken, looking over the internet and even at the second hand market in the USA where the meter originates from I was unable to find the required part to get the meter operational again. Additional the installed Garmin fishfinder started to leak around the hull support beginning of the year. The plan was to remove the fishfinder/depth meter and reinstall it and to buy a new speed sensor. When the boat was out of the water and trying to remove the depth meter this was not as easy as expected, I presumed that the unit was placed with caulking into the hull, unfortunately this was not the case , the unit was installed with epoxy therefore I ended up with drilling the unit out of the hull, small drill around the shaft of the unit placed in the hull. The thread was damaged but not beyond the point that the system could not be used anymore.
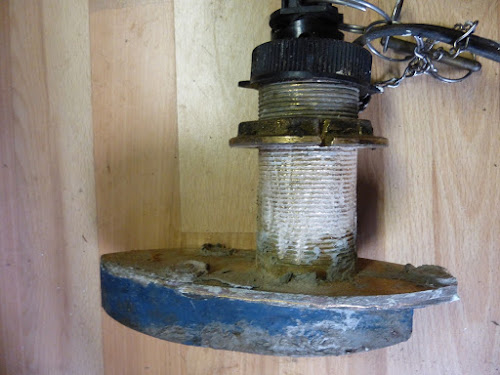
Since the speed indicator was broken as well I bought a new system where I had the speed and depth in one unit. I'm not into catching fish.
The holes in the hull of the original units were closed with a plug and the new units were installed.
For the speed indicator this was rather simple drilling a hole of the correct seize and fitting the new unit flat against the hull with caulking, although under an angle the wheel will be rotated by the water flow. This unit was placed under the small hatch I have in the main cabin for easy access incase the wheel would be blocked due to growth or dirt. One can then remove the shaft with wheel and place a temporarily cap on the unit fitted into the hull to perform maintenance on the actual speed pick up, wheel.
The advantage of this unit, Manufacturer Clipper , is that the actual speed indication can be adjusted , this way, even if the speed indication is not correct after installation it can be corrected on the display unit. These days there are apps. available on the telephone where one can check the actual ships speed and the speed indicator can so be adjusting to the correct value.
The depth meter was a little more work since it needs to point straight downwards otherwise you would not get the correct measurement under the keel. To compensate the angle from the hull a small piece of wood was installed inside to fit the depth meter straight into the hull pointing downwards.
On the outside an original, from the manufacturer supplied, under the same angle, housing for the depth sensor was installed as well. The wooden block was pre drilled with the holes in the same position as the outside unit. The wooden block was placed on the hull and the holes were drilled through the bottom of the boat.
All was then degreased and was installed with caulking. Afterwards the inside hull was painted again.
On the outside as can be seen from the next picture both units are close together and close to the keel so that no damage can be expected to the units when the boat will be lifted out of the water the next time . by means of a boat car or slings.
The actual display unit was placed next to the maneuvering stand in a small wooden case.
Rudder Indicator
Since the speed indicator in the center of the maneuvering consol was removed I ended up with a big hole. To make sailing and maneuvering with the boat a bit easier I installed a rudder indicator.
Pick up unit
This is not a difficult installation a support needs to be made on the right height a connection between the rudder stock and the pick up and last but not least some wires to be ran between the pick up and the actual rudder indicator in the console as well as a power supply. Following the manufacturer's instructions this whole installation did not took more than a few hours.
Rudder indicator
Tent and window cover
When the boat was bought there was a tent placed to cover the steering cabin completely. This tent was in a bad condition and a new one was made in house by my neighbor Jan who helped me over the years with restoring the boat. Going over several web sides covering the Storebro 34 I noticed that originally there is no tent to cover the steering cabin, this also explains to me the two large drains in the steering cabin floor. The pictures contain some dimensions and additional text as further explanation, but as with any boat port and starboard side might not be the exact same length and height.
The old tent was not used as example for the new tent since the windows in the tent did not lined up with the metal supports which keep the tent up and in position, it was just used as an idea how to fabricate the new tent. Materials were bought and with the help of U-Tube short films a plan was made to fabricate the tent. The metal support was kept as original and positioned the same way onto the deck. One disadvantage of this tent is when it is closed that during arrival and departure the aft deck is difficult to reach since the railings on the aft cabin are covered by the tent so there is no way one can keep " One hand for the boat and one for yourself"
The tent is connected to the hard top by way of a aluminium rail with a groove where a tendon ( Cord) is placed in, This tendon is sowed to a strong material where the actual tent is sowed on.
The connection to the hard top is made with a zipper to be able to remove the complete tent when required, mainly during a sunny day. The zipper is also connected to strong material to give it a reinforcement for holding the zipper onto the tent.
To make sure that not all the tension of the tent is placed onto the zipper a Velcro connection is made between both sides of the zipper,on side onto the rail in the roof other onto the tent.
The tent is kept in position and giving the required height by two round metal bars which are on a sliding rail which is mounted on the roof of the aft cabin.
The tent is hold into position around these round bars by means of tent material and a full length zipper, this way the tent can be removed from the support bars .
The side windows are now made in line with the tent supports, which gives it a nice look from outside, originally the supports could be seen from the outside through the window.
On positions of the corners and where tension is expected where the tent touches the hand rails additional tent material was sowed onto the tent at the inside this way expecting that the tent will last longer.
The tent around the forward side windows I would make it different if a new tent is made in the future. I would make it a straight line with the roof , which would give it a nicer look in my opinion, this was not done since we followed the original design at this point. One challenge could be mounting the tent clips under the roof, difficult drilling a hole.
The height of the tent was kept the same as the height of the roof of the steering cabin.
The aft window can be completely opened for a not so sunny day but still warm enough to sit dry while sailing. This is accomplished by a zipper on either side of the window.
The tent is made in such a way that on the aft side it hardly touches the hand rail and in such a way preventing rubbing of the tent against the hand rail and this gives the tent a straight line from the top to the bottom at the aft side.
Below some pictures with dimensions. At the aft side both corners straps are placed to give some tension on the tent and to keep it in place , supports are mounted onto the aft cabin roof.
Over the last few years I noticed that the wood in the steering cabin started to discolor again , my boat in the marina faces south, asking my friendly neighbor Jan again if he could make a window cover for the steering cabin.This cover goes over the forward window and side windows. I admit it is getting a bit dark inside but on the other hand temperatures stay a bit lower and the discoloring of the wood will be slower.Minor advantage the sliding side window is now also covered which will prevent from water entering inside.
The cover is as with the tent connected with clips onto the wood a few at the front and the sides, to make it easier for fabrication the window wipers are placed on top of the material.
On the side the cover is placed under the tent so that the gap between the tent and the wood is minimized. In the past I had some ingress of rainwater and even snow depending off course on the wind direction.
Where the cover meets the tent the cover does have so called tent rings , this way the clips hold the cover in place and under a minimum of tension.
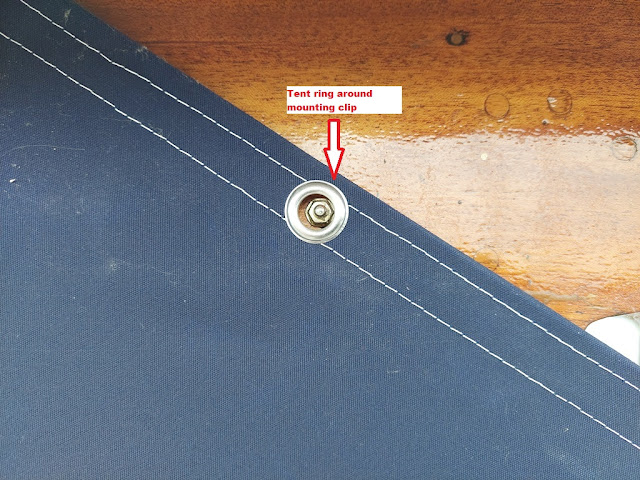